Precision CNC Milling for Complex Parts
Providing accurate and reliable CNC milling services for intricate geometries across aerospace, automotive, and other industries.
* Strict tolerance of ±0.005mm
* Over 100 kinds of certified materials
* Customized surface
* Fast service, with the fastest delivery in 3 days
* Document confidentiality
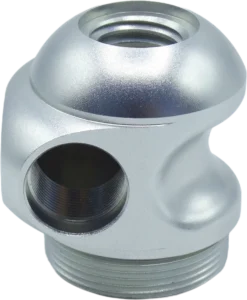
What is CNC Milling?
——————
CNC milling is a precise and versatile machining process where material is removed using computer-controlled machines to create complex parts. This technology is widely used across industries like aerospace, automotive, and electronics to produce high-quality components with intricate shapes and tight tolerances.
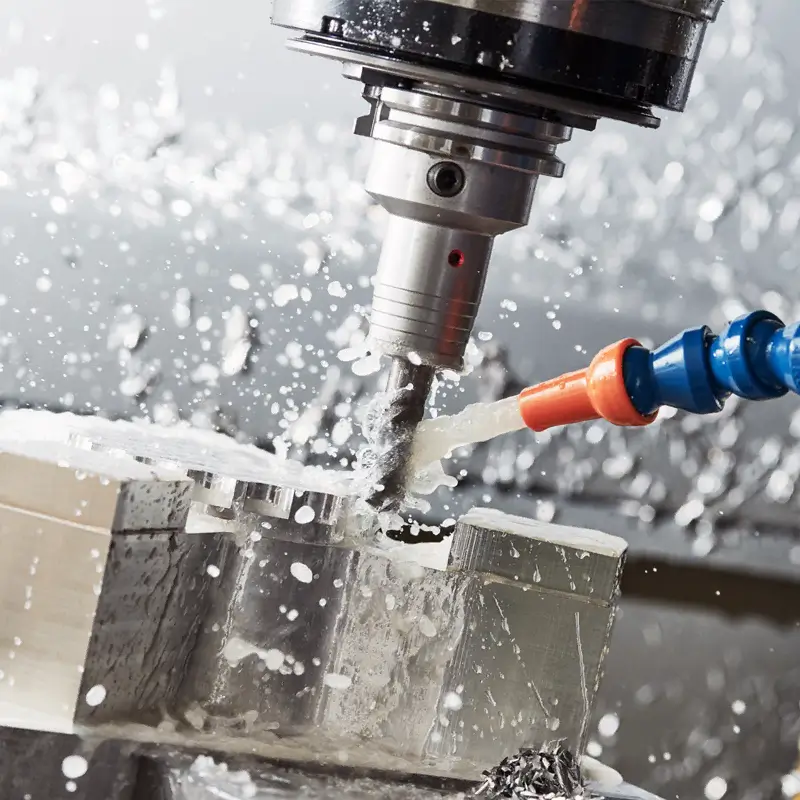
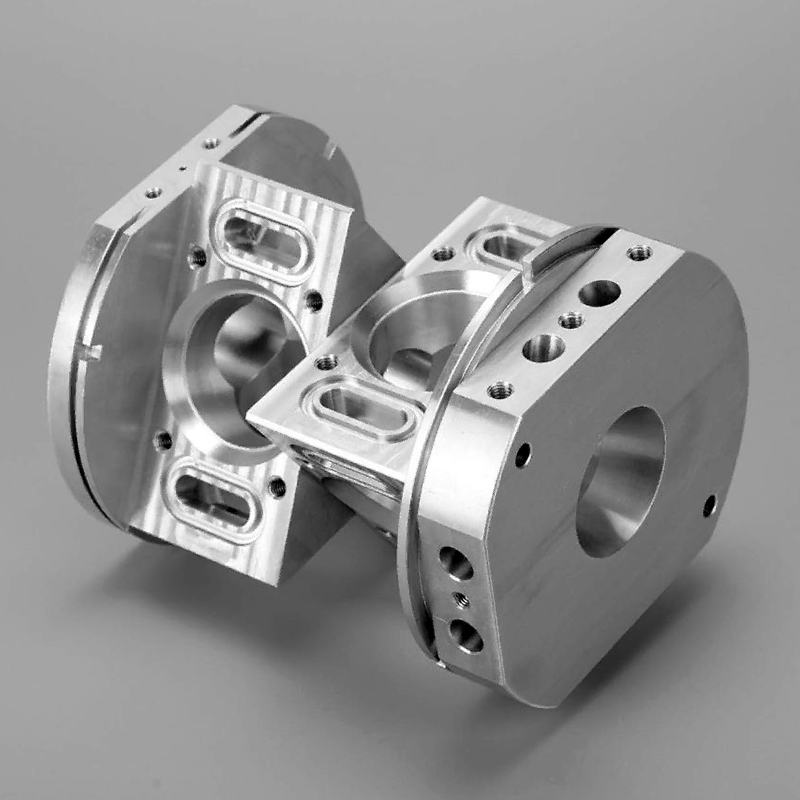
Our CNC Milling Capabilities
——————
Our CNC milling services are designed to meet the most demanding industry requirements with precision and reliability. Using a variety of advanced CNC milling machines, including 3-axis, 4-axis, and 5-axis models, we can handle complex geometries and intricate designs with exceptional accuracy. With tolerances as tight as ±0.01mm, we ensure every part meets your exact specifications.
We are proficient in machining a wide range of materials, from metals like aluminum, stainless steel, and titanium to engineering plastics such as POM, ABS, and PEEK. Whether you need prototypes, small-batch production, or large-scale manufacturing, our experienced team delivers high-quality results with fast turnaround times, typically within 5–7 business days.
CNC Milling Tolerances and Surface Finishes
At JXD-Machining, we ensure the quality and consistency of our CNC milling processes through precise tolerances and professional surface finish standards. By adhering to these principles, we minimize potential errors and avoid costly defects in final products.
Tolerances: Tolerances represent the acceptable deviation from specified dimensions when machining parts. These play a critical role in setting up machines and producing custom-milled components.
At JXD-Machining, we adhere to ISO 2768 standards for both plastic and metal parts, ensuring our products meet the highest quality benchmarks. Typically, our CNC milling tolerances range from ±0.005 inches (±0.125 mm) to as tight as ±0.002 inches (±0.05 mm) or even ±0.01 mm for highly precise applications.
Surface Finish Standards: The surface finish of machined parts is crucial for both functionality and aesthetics.
We offer a variety of surface roughness options to meet your specific requirements:
• Standard Machined Finish: Ra 3.2–1.6 μm
• Smooth Machined Finish: Ra 1.6–0.8 μm
• Ultra-Fine Finish: Ra 0.8–0.2 μm
Applications of CNC Milled Parts
CNC milling plays a crucial role in manufacturing high-precision components across various industries. Below are some of the most common applications:
✔ Medical Industry
Used to produce orthopedic implants, surgical instruments, and other precision components for healthcare applications.
✔ Electronics
Manufacturing electronic hardware, enclosures, metal brackets, panels, engraved parts, and intricate components essential for electronic devices.
✔ Defense and Military
3-axis and 5-axis CNC machines create custom-milled parts for military aircraft, vehicles, weapons, and submarine systems.
✔ Automotive
CNC milling is indispensable for producing custom automotive components, including gearboxes, turbochargers, and interior panels.
✔ Aerospace
Aircraft components such as engine parts, gear systems, hydraulic manifolds, landing gear, and electrical housings rely on CNC milling for precision and reliability.
✔ Food Processing Equipment
Specialized components for mixers, grinders, crushers, and cleaning equipment in food production are designed using CNC milling technology.
✔ Machine Tools
The tooling industry requires CNC milling for parts like fasteners, fittings, shafts, and hydraulic or mechanical components critical for various equipment.
High-Quality Materials for CNC Machining
We provide high-quality metals, plastics, and composite materials for CNC machining, capable of meeting a wide variety of application requirements, including but not limited to:
Metal Materials
Plastic and Composite Materials
Surface Finishing for CNC Machined Parts
JXD-Machining provides diverse surface finishing options to enhance the appearance, durability, and performance of CNC machined parts, meeting both functional and aesthetic needs.
Surface Finishing Options for CNC Parts
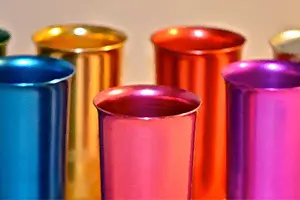
Anodizing
A durable and corrosion-resistant finish that enhances the aluminum part’s surface while providing an aesthetic appearance. Ideal for improving wear resistance and offering a wide range of color options.
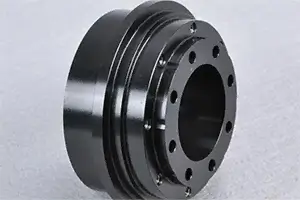
Black Oxide
A chemical coating that provides moderate corrosion resistance and a sleek black appearance, often used for steel parts to reduce glare and improve aesthetic appeal.
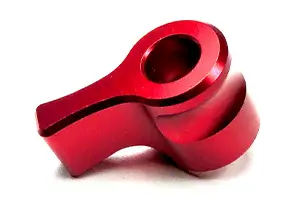
Sandblasting + Type II Anodizing
Combines a matte finish from sandblasting with Type II anodizing to create a smooth, uniform surface that is corrosion-resistant and visually appealing.
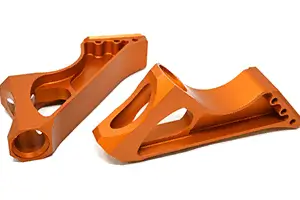
Sandblasting + Type III Anodizing (Hard Coat)
A more robust version of anodizing combined with sandblasting, offering excellent wear and corrosion resistance for applications requiring durability under harsh conditions.
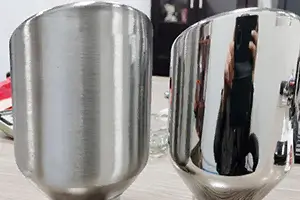
Polishing
Enhances the surface of parts by removing minor imperfections, resulting in a smooth and shiny finish that improves aesthetic appeal and surface cleanliness.
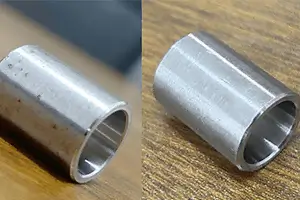
Passivation
Passivation enhances corrosion resistance by removing surface contaminants and forming a protective oxide layer. Ideal for stainless steel, it ensures durability, cleanliness, and long-term performance in industries like aerospace and medical devices.
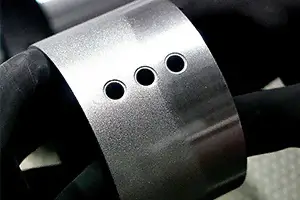
Sandblasting
Uses abrasive particles to create a uniform matte texture on the part’s surface, ideal for preparing parts for subsequent coatings or achieving a visually attractive finish.
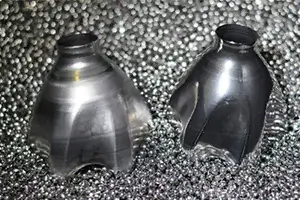
Tumbling
A mechanical finishing process that smoothens and polishes parts by rotating them in a tumbler with abrasives, suitable for deburring and improving surface texture.
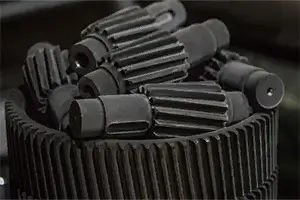
Heat Treatment
Enhances the mechanical properties of metal parts, such as hardness, toughness, and wear resistance, by heating and cooling them under controlled conditions.
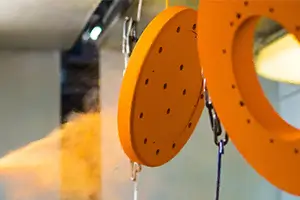
Powder Coating
Applies a durable and uniform layer of colored polymer powder, offering excellent protection against corrosion, UV damage, and general wear and tear.

Electroplating
A process of depositing a thin metal layer, such as nickel or chrome, onto a part’s surface to improve its appearance, corrosion resistance, and durability.
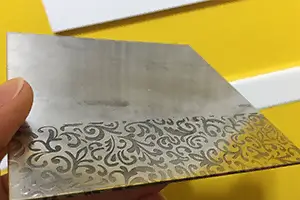
Laser Engraving
Uses focused laser beams to etch designs, text, or markings onto parts with high precision, providing permanent and highly detailed customizations.
Learn more about our metal and plastic surface finishing capabilities here.
CNC Milling FAQ
1. What is CNC Milling?
CNC milling is a subtractive manufacturing process that removes excess material from a workpiece using computer numerical control (CNC) technology. The process begins with a CAD file, which generates a toolpath to guide the cutting tools and shape the workpiece with precision.
2. What Tools Are Commonly Used in CNC Milling?
End mills are the most commonly used tools for a variety of operations. Other popular tools include ball-end mills (for complex curved surfaces), chamfer mills (for edge finishing), and dovetail cutters (for slots and grooves).
3. What Are the Surface Finishing Options for CNC Milling?
CNC milling allows for a range of surface finishing options to enhance durability, corrosion resistance, and aesthetics. Common finishes include anodizing, polishing, sandblasting, powder coating, and plating. The best option depends on the specific project requirements.
4. What is the Difference Between CNC Turning and CNC Milling?
CNC turning involves rotating the workpiece while a stationary cutting tool shapes it, making it ideal for cylindrical parts. CNC milling, on the other hand, keeps the workpiece stationary and moves the cutting tool to create complex shapes, including flat and curved surfaces.
5. What is 5-Axis CNC Milling?
5-axis CNC milling allows cutting tools to move in three linear directions (X, Y, Z) and rotate around two additional axes, enabling access to more angles and surfaces of the material. This advanced capability supports the production of highly complex parts, improves precision, and increases efficiency compared to 3-axis machines.