Custom Precision Metal Parts with Certified Quality and On-Time Delivery
• Precision Manufacturing
• On-Time Delivery Guarantee
• Tailored for Your Needs
• Customer data security
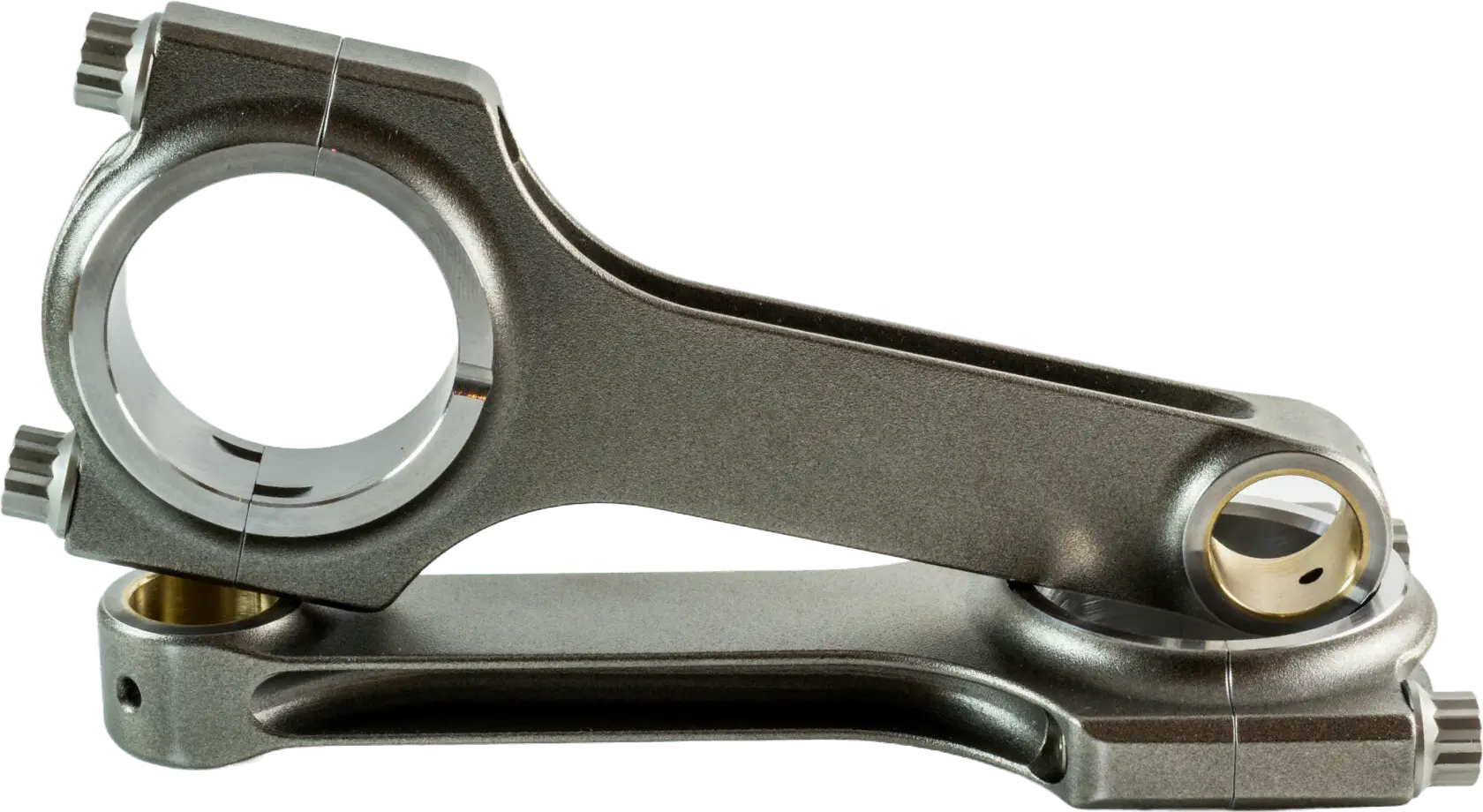
What is Die Casting?
——————
Die casting is a manufacturing process where molten metal is injected into a mold under high pressure to produce precise, complex metal parts. This efficient and versatile process is widely used in industries requiring high-quality components with tight tolerances and smooth finishes. Common materials include aluminum, zinc, and magnesium alloys, each offering unique benefits for different applications.
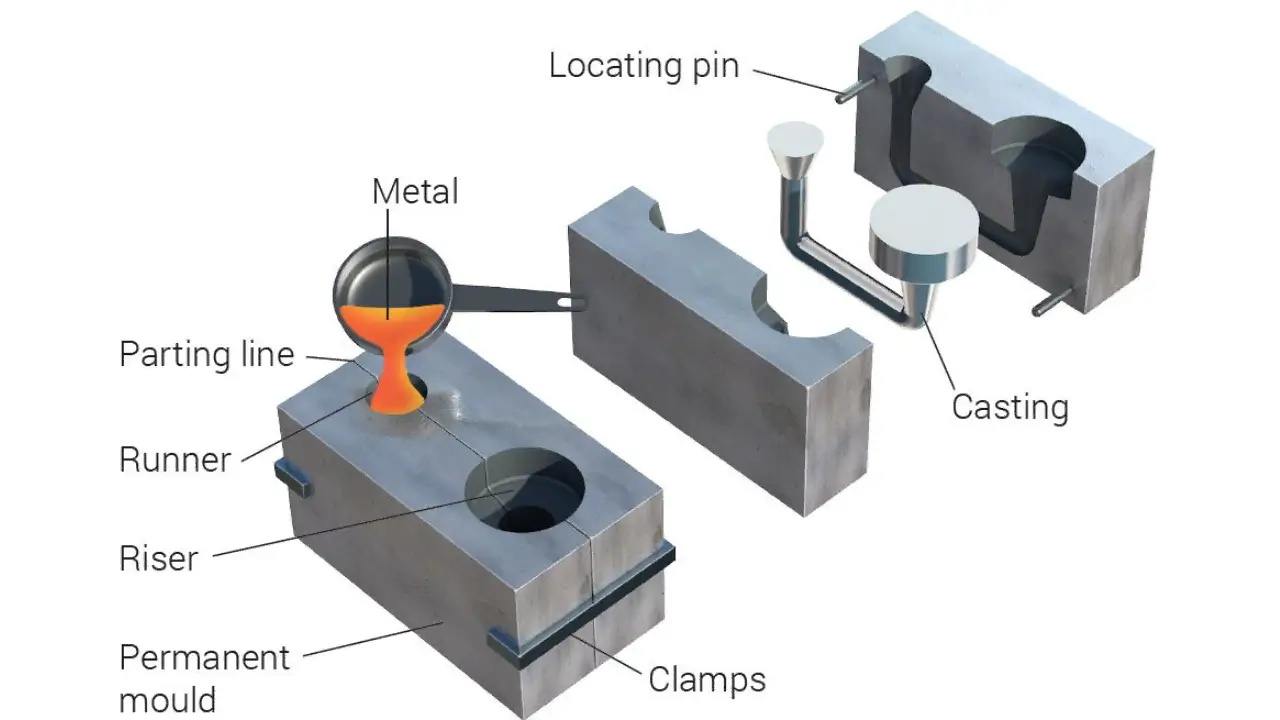
Types of Die Casting Processes
High-Pressure Die Casting (HPDC)
Ideal for mass production of lightweight, intricate components, HPDC is commonly used in the automotive and electronics industries. Its ability to produce parts with excellent surface quality and dimensional accuracy makes it a go-to choice for precision manufacturing.
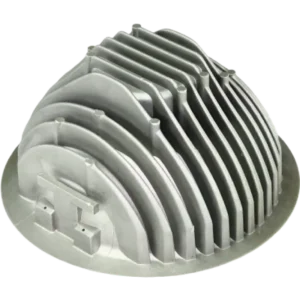
Low-Pressure Die Casting (LPDC)
Designed for larger, high-strength components, LPDC is widely employed in aerospace and heavy machinery applications. This process ensures exceptional mechanical properties and durability.
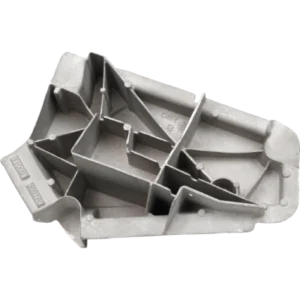
Gravity Die Casting
Perfect for medium-volume production, gravity die casting uses natural gravity to fill molds. It is well-suited for parts like valve housings, engine blocks, and structural components requiring strength and consistency.
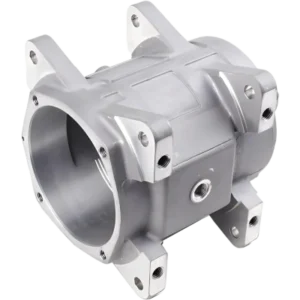
Our Die-Casting Capabilities
As a professional die-casting manufacturer, we provide end-to-end services, from design to mass production, to meet the demand for high-quality die-cast components.
Capability | Specifications |
---|---|
Minimum Part Weight | 0.02 kg (Suitable for high-precision manufacturing of small components like electronic housings) |
Maximum Part Weight | 10 kg (Supports the production of larger components such as automotive or industrial parts) |
Minimum Part Dimensions | Ø10 mm × 2 mm (Ideal for small, complex structures) |
Maximum Part Dimensions | 500 mm × 800 mm (Fits large housings and industrial equipment components) |
Minimum Wall Thickness | 0.6 mm (Enables thin-wall part designs, reducing material costs and weight) |
Maximum Wall Thickness | 10 mm (Suitable for thick-walled components, ensuring strength and durability) |
Material Options | Aluminum Alloys, Zinc Alloys, Magnesium Alloys (Tailored to diverse industries and applications) |
Quality Assurance | ISO 9001 & IATF 16949 Certified (Strict quality control for reliability and consistency) |
Production Volume | Starting at 500 pieces, flexible for both small and large-scale production needs |
Mold Development Lead Time | 2 - 4 weeks (Quick response to customer requirements, shortening delivery cycles) |
Surface Finishing Options | Polishing, Electroplating, Coating, Anodizing, etc. (Combining functionality and aesthetics) |
Applications of Die Casting
Our die casting services cater to a wide range of industries, delivering reliable, precision-engineered components for the most demanding applications. Key areas include
• Automotive: Engine blocks, transmission cases, brake systems.
• Electronics: Heat sinks, housings, and connectors.
• Aerospace: Aircraft structural components, turbine casings.
• Industrial Equipment: Pump bodies, valve parts, and gears.
Advantages of Die Casting
Why Choose Us for Die-Casting Solutions?
Comprehensive Capabilities
• From micro-sized electronic housings to large automotive components, our manufacturing range covers various industries with precision.
Strict Quality Control
• Equipped with advanced testing methods such as X-ray Inspection, CMM Measurements, and adherence to international certifications like ISO 9001 and IATF 16949, we ensure every product meets the highest standards.
Custom Solutions
• Collaborate with our experienced engineers to optimize designs, select the best materials, and achieve cost-effective production.
Advanced Equipment
• Utilizing state-of-the-art die-casting machines ranging from 160T to 800T, we meet the demands of diverse project requirements.
Surface Treatment Expertise
• Enhance your product with tailored surface finishes like polishing, anodizing, or coating, combining functionality with superior aesthetics.
Industry Applications
• Our products are widely used in automotive components, industrial machinery, consumer electronics, and medical devices.
Fast Turnaround
• Mold development in 2-4 weeks, with rapid prototyping and reliable mass production, ensuring your products hit the market faster.
Lower Costs, Better Value
• Through thin-wall casting and high-efficiency processes, we help you reduce material waste and achieve competitive pricing without compromising quality.
FAQ
1. What materials do you offer for die casting?
We specialize in aluminum, zinc, and magnesium alloys to meet diverse application needs.
2. Can you assist with design optimization?
Yes, our engineering team works closely with you to ensure efficient and cost-effective designs.
3. What are your lead times?
Production typically takes 2–6 weeks depending on complexity and volume.
4. Do you provide surface treatments?
Absolutely. We offer a wide range of finishing options including polishing, anodizing, and painting.
5. What industries do you serve?
We serve automotive, aerospace, electronics, and industrial sectors globally.