Custom Sheet Metal Fabrication Services

JXD provides one-stop sheet metal fabrication services
JXD offers comprehensive sheet metal fabrication solutions tailored to your specific needs. With advanced technology, precision craftsmanship, and a commitment to quality, we deliver durable and cost-effective custom parts for industries worldwide.
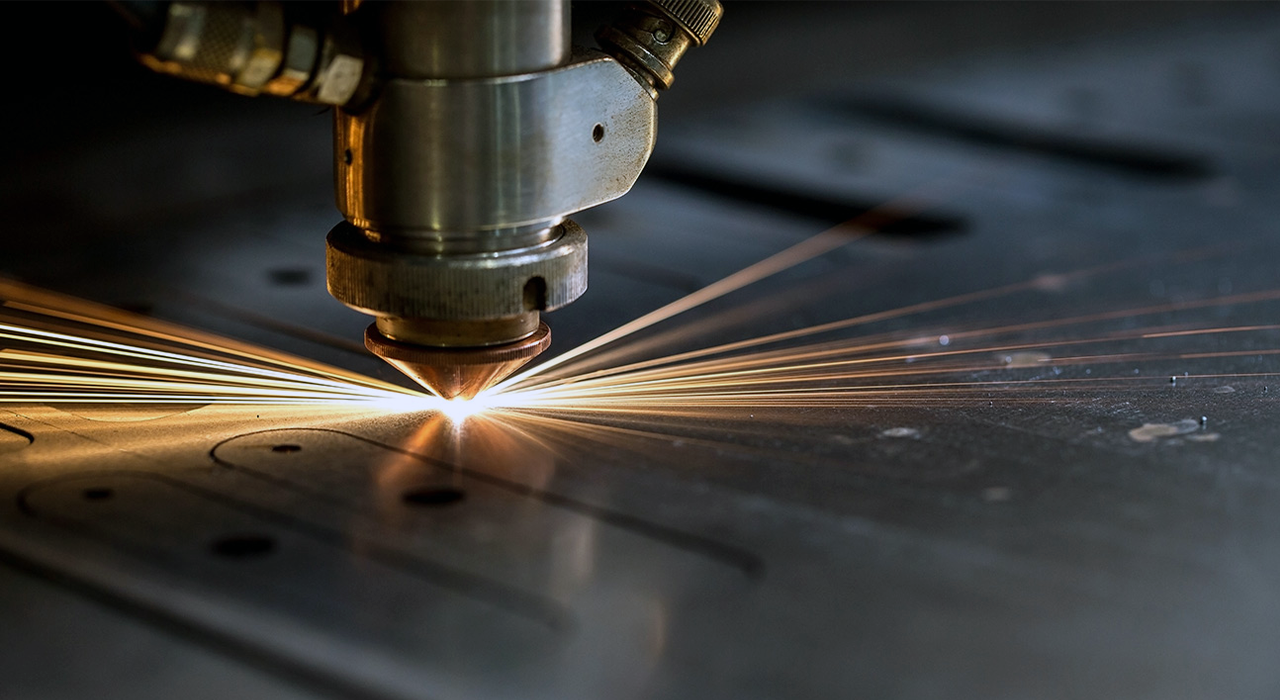
Laser Cutting
An efficient process for cutting intricate designs with high precision. Ideal for stainless steel, aluminum, and other metals, laser cutting minimizes waste and supports both prototypes and large-scale production.
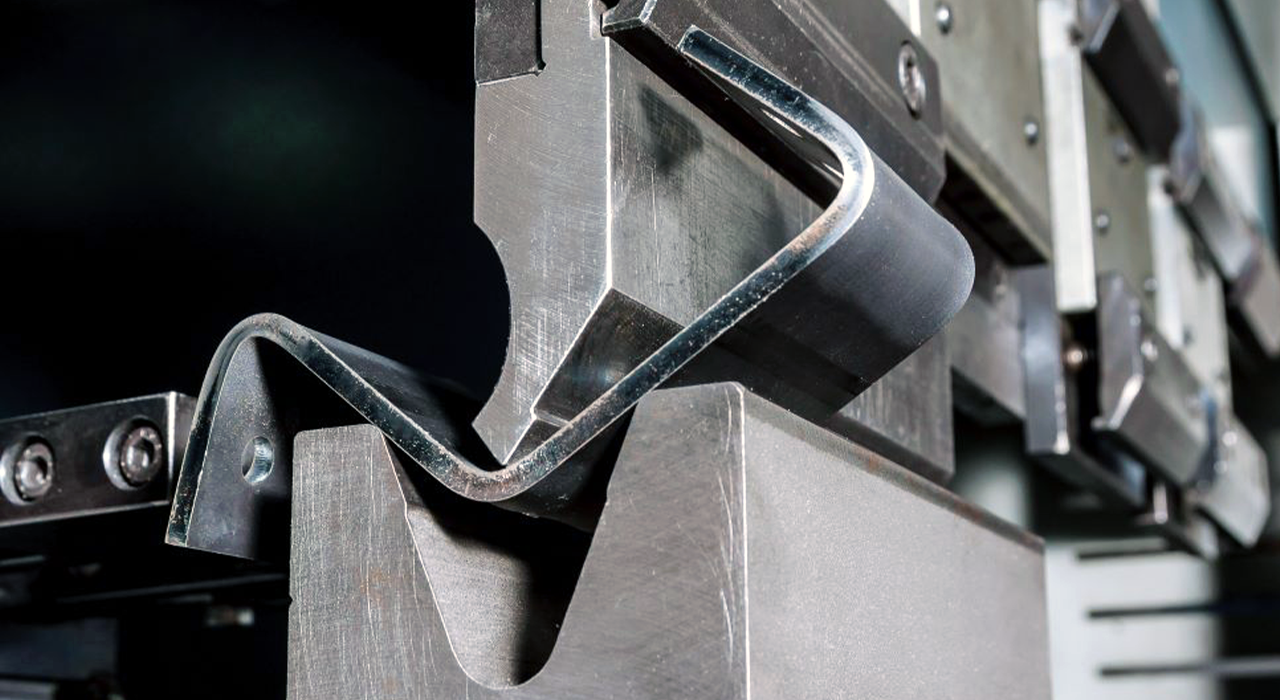
Bending
An efficient process for cutting CNC-controlled bending ensures accurate angles and consistent results for parts of various sizes and complexities. This process is widely used for creating structural and aesthetic components.

Welding
We provide TIG, MIG, and spot welding for seamless and strong metal joints. Welding is perfect for structural assemblies, ensuring durability and clean finishes for both visible and functional parts.
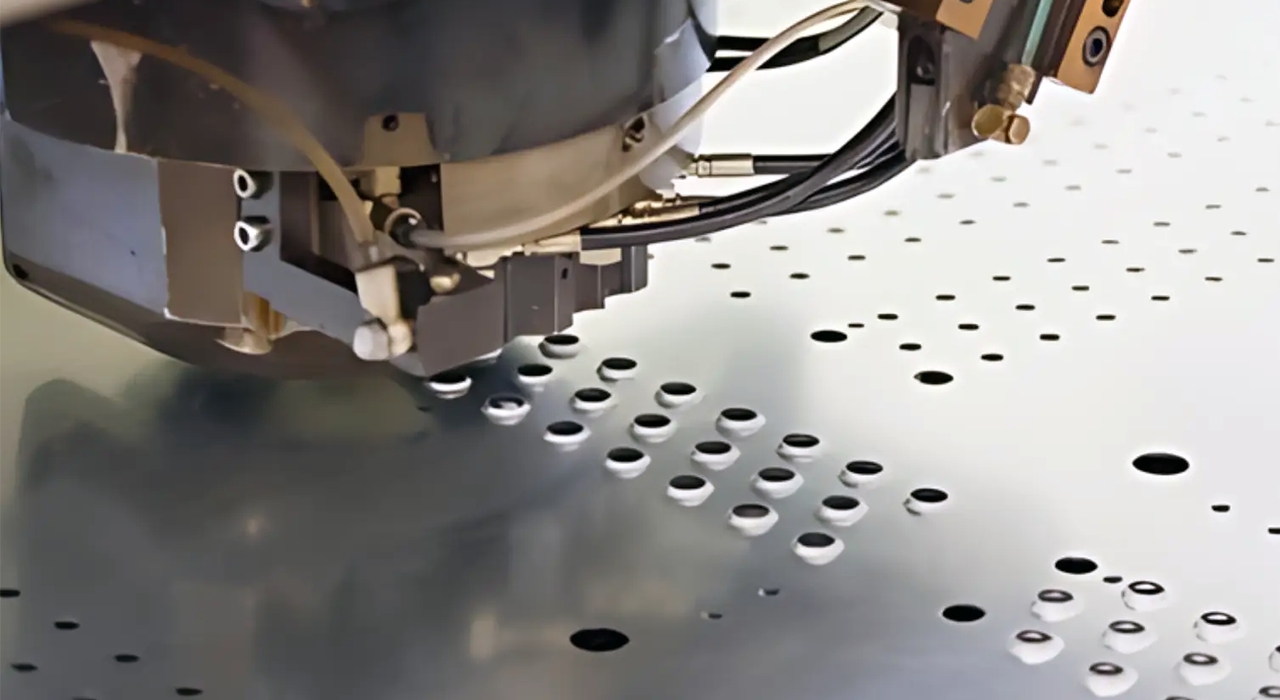
Punching
Efficiently creates holes, slots, and custom patterns with speed and accuracy. Suitable for batch production, punching supports a range of metal thicknesses and is ideal for detailed designs.
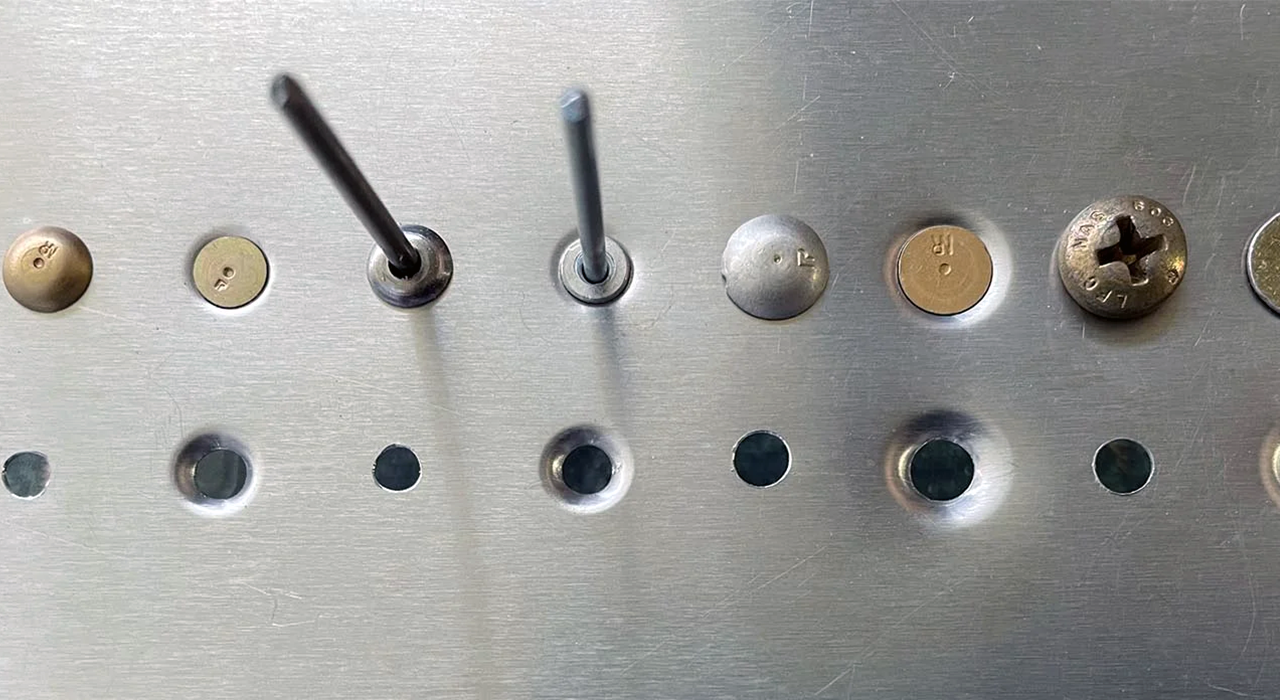
Riveting
A quick and reliable method for joining components, riveting is ideal for lightweight assemblies requiring flexibility and vibration resistance. Perfect for both temporary and permanent applications.
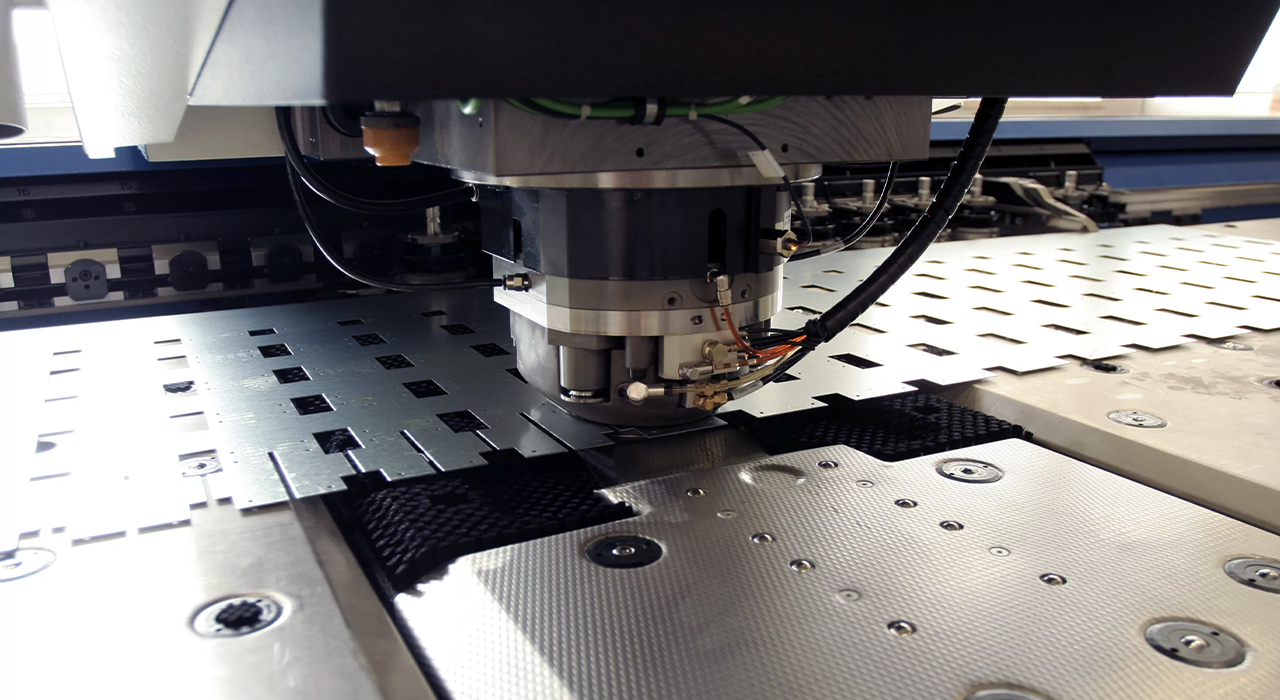
Stamping
High-speed stamping delivers durable, intricately shaped parts at scale. This process is ideal for mass production of lightweight yet strong components with uniform quality.
Sheet Metal Design Guidelines
A well-thought-out design is essential for efficient sheet metal fabrication and high-quality products. Here are key considerations:
1. Material Selection
Choose suitable materials such as stainless steel, aluminum alloy, carbon steel, or copper, balancing strength, weight, and cost.
2. Bend Radius
Maintain appropriate bend radius to prevent material cracking or deformation during forming.
3. Hole Size and Placement
Ensure hole diameters are at least 1.5 times the material thickness, with edge distances no less than 2 times the material thickness.
4. Welding Considerations
Design joints with adequate space for welding tools, ensuring strength and clean finishes.
5. Surface Treatment Compatibility
Plan for finishes like powder coating, anodizing, or polishing based on functionality and appearance requirements.
6. Assembly Requirements
Account for space needed for bolts, rivets, or other fastening methods to streamline final assembly.
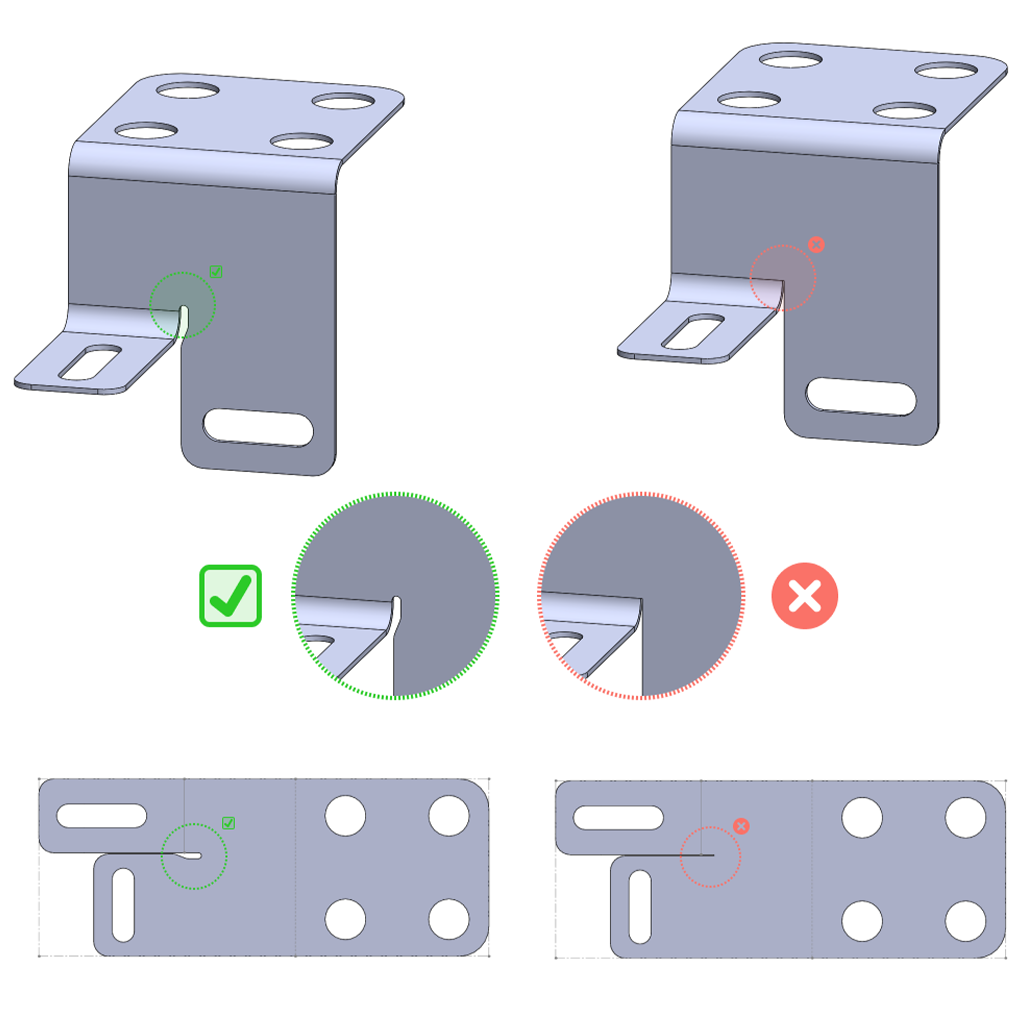
Surface Finishing for CNC Machined Parts
JXD-Machining provides diverse surface finishing options to enhance the appearance, durability, and performance of CNC machined parts, meeting both functional and aesthetic needs.
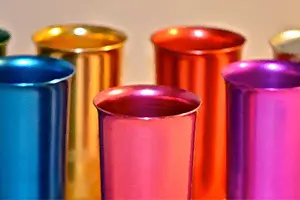
Anodizing
A durable and corrosion-resistant finish that enhances the aluminum part’s surface while providing an aesthetic appearance. Ideal for improving wear resistance and offering a wide range of color options.
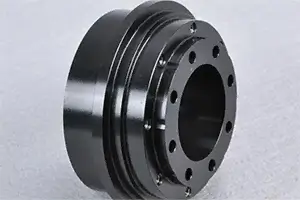
Black Oxide
A chemical coating that provides moderate corrosion resistance and a sleek black appearance, often used for steel parts to reduce glare and improve aesthetic appeal.
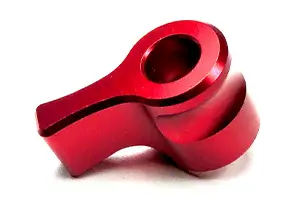
Sandblasting + Type II Anodizing
Combines a matte finish from sandblasting with Type II anodizing to create a smooth, uniform surface that is corrosion-resistant and visually appealing.
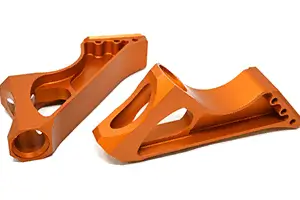
Sandblasting + Type III Anodizing (Hard Coat)
A more robust version of anodizing combined with sandblasting, offering excellent wear and corrosion resistance for applications requiring durability under harsh conditions.
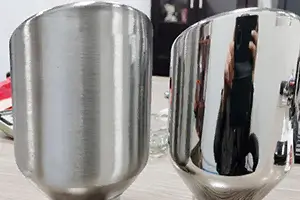
Polishing
Enhances the surface of parts by removing minor imperfections, resulting in a smooth and shiny finish that improves aesthetic appeal and surface cleanliness.
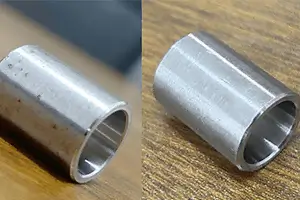
Passivation
Passivation enhances corrosion resistance by removing surface contaminants and forming a protective oxide layer. Ideal for stainless steel, it ensures durability, cleanliness, and long-term performance in industries like aerospace and medical devices.
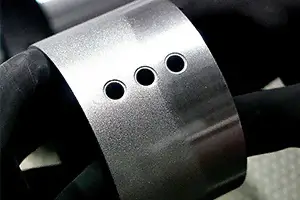
Sandblasting
Uses abrasive particles to create a uniform matte texture on the part’s surface, ideal for preparing parts for subsequent coatings or achieving a visually attractive finish.
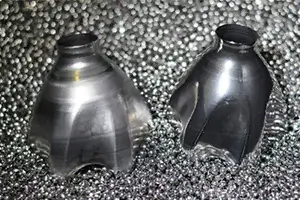
Tumbling
A mechanical finishing process that smoothens and polishes parts by rotating them in a tumbler with abrasives, suitable for deburring and improving surface texture.
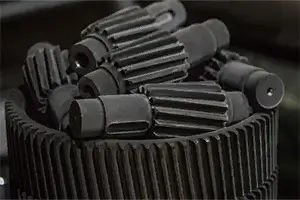
Heat Treatment
Enhances the mechanical properties of metal parts, such as hardness, toughness, and wear resistance, by heating and cooling them under controlled conditions.
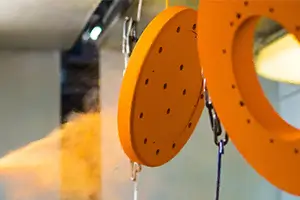
Powder Coating
Applies a durable and uniform layer of colored polymer powder, offering excellent protection against corrosion, UV damage, and general wear and tear.

Electroplating
A process of depositing a thin metal layer, such as nickel or chrome, onto a part’s surface to improve its appearance, corrosion resistance, and durability.
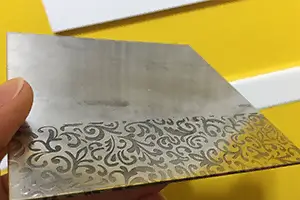
Laser Engraving
Uses focused laser beams to etch designs, text, or markings onto parts with high precision, providing permanent and highly detailed customizations.
FAQ
1. What materials do you work with?
We handle stainless steel, aluminum, carbon steel, copper, and more.
2. What are your minimum and maximum sizes for fabrication?
Our capabilities range from 0.5 mm to 20 mm in thickness, with maximum dimensions of 3000 × 1500 mm.
3. Do you accept low-volume orders?
Yes, we offer flexible production options, from prototypes to large-scale manufacturing.
4. What is your typical lead time?
Samples are ready within 3 days, while bulk orders typically take 7-15 days, depending on complexity.
5. Do you provide surface treatment services?
Yes, we offer powder coating, anodizing, polishing, brushing, and more.
6. How can I request a quote?
Upload your design files or share your requirements, and our engineers will provide a detailed quote within 3 hours.