About the Aluminum
Aluminum is a highly versatile and lightweight material, making it a top choice for industries requiring components with a high strength-to-weight ratio. Known for its excellent machinability, natural corrosion resistance, and recyclability, aluminum is widely used in aerospace, automotive, electronics, and construction applications. Its ability to combine durability with aesthetic finishes makes it ideal for both functional and decorative parts.
· Lightweight yet Strong: Aluminum offers exceptional strength while maintaining a low weight, reducing overall part mass without compromising durability.
· Corrosion Resistance: Naturally resistant to oxidation, aluminum performs reliably in harsh environments, including marine and industrial settings.
· Thermal and Electrical Conductivity: Its superior heat dissipation and electrical properties make it perfect for electronic enclosures, heat sinks, and power systems.
· Wide Range of Finishes: Compatible with anodizing, powder coating, polishing, and more, aluminum can achieve both functional and aesthetic goals.
· Eco-Friendly: Aluminum is 100% recyclable without losing its properties, making it a sustainable choice for modern manufacturing needs.
· Excellent Machinability: Supports complex designs and tight tolerances, ensuring efficiency in production and reduced lead times.
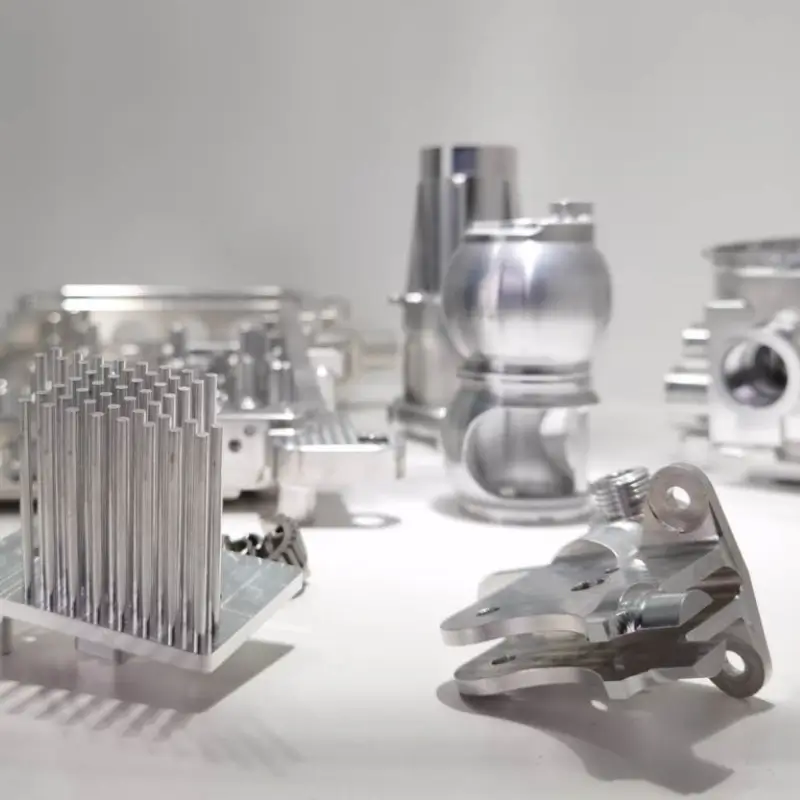
Comparison of Common Aluminum Aloys
Aluminum Grade | Cost | Tensile Strength (Ultimate) | Max Operating Temperature | Elongation | Hardness | Weldability | Thermal Conductivity | Common Applications |
---|---|---|---|---|---|---|---|---|
Aluminum 6061 - T6 | $ | 291–320 MPa | 130–150°C | 12–17% | 60 HRB | Excellent | 152–169 W/(m·°C) | Automotive, marine, electrical systems |
Aluminum 7075 - T6 | $$$ | 434–580 MPa | Up to 100°C | 2–11% | 79–86 HRB | Limited | 131–137 W/(m·°C) | Aerospace, marine, high-performance parts |
Aluminum 5083 - H111 | $$ | 270–350 MPa | 80–100°C | 0.13 | 74 HV | Excellent | 118–128 W/(m·°C) | Marine industry, pressure vessels |
Aluminum 6082 | $ | 140–340 MPa | 130–150°C | 6.3–18% | 35–56 HRB | Excellent | 160–180 W/(m·°C) | Structural components, pylons |
Aluminum 2024 - T4 | $$ | 400–450 MPa | 120°C | 10–20% | 70 HRB | Limited | 120–140 W/(m·°C) | Aerospace, military, and transport systems |
Aluminum 5052 - H32 | $ | 193–228 MPa | 65–90°C | 5–12% | 60 HRB | Excellent | 138–150 W/(m·°C) | Marine, automotive, and industrial applications |
Aluminum 1100 | $ | 90–125 MPa | Up to 120°C | 30–40% | 35 HB | Excellent | 222 W/(m·°C) | Food industry, chemical equipment |
Optimized Aluminum Alloys for CNC Machining
Aluminum 6061-T6
A heat-treatable alloy known for its exceptional strength and corrosion resistance. Featuring magnesium and silicon as key alloying elements, the T6 temper signifies solution heat-treated and artificially aged for enhanced properties. Aluminum 6061-T6 is widely used in aerospace, automotive, and structural applications due to its durability and excellent weldability.
• High strength with corrosion resistance
• Weldable and versatile for various applications
• Ideal for aerospace, automotive, and construction industries
Aluminum 7075-T6
Renowned for its exceptional strength and hardness, 7075-T6 aluminum is designed for high-performance parts requiring durability under heavy loads. It’s lightweight, resistant to corrosion, and can be anodized for improved surface protection and aesthetics. This makes it a popular choice for aerospace and defense applications.
• High strength-to-weight ratio
• Excellent wear and corrosion resistance
• Common in aerospace, marine, and military components
Aluminum 5083-H111
A non-heat-treatable alloy with superior corrosion resistance, especially in marine environments. Its high ductility, moderate strength, and excellent weldability make it an ideal choice for unfired pressure vessels, cryogenic tanks, and marine structures.
• Outstanding seawater resistance
• Suitable for cryogenic and marine applications
• Excellent ductility and weldability
Aluminum 6082
A medium-strength alloy prized for its corrosion resistance and machinability. With magnesium and silicon as its primary alloying elements, it’s well-suited for highly stressed structural applications. Aluminum 6082 is particularly popular in transportation and structural engineering, including bridges and load-bearing components.
• Excellent balance of strength and corrosion resistance
• Great for structural and transport applications
• Weldable with good formability
Surface Finishing for CNC Machined Parts
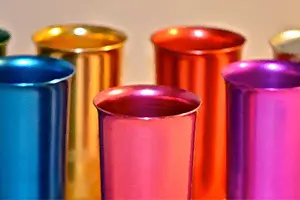
Anodizing
A durable and corrosion-resistant finish that enhances the aluminum part’s surface while providing an aesthetic appearance. Ideal for improving wear resistance and offering a wide range of color options.
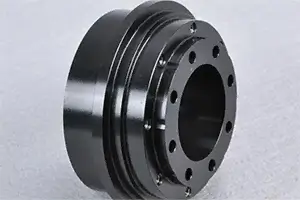
Black Oxide
A chemical coating that provides moderate corrosion resistance and a sleek black appearance, often used for steel parts to reduce glare and improve aesthetic appeal.
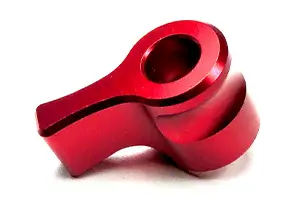
Sandblasting + Type II Anodizing
Combines a matte finish from sandblasting with Type II anodizing to create a smooth, uniform surface that is corrosion-resistant and visually appealing.
Sandblasting + Type III Anodizing (Hard Coat)
A more robust version of anodizing combined with sandblasting, offering excellent wear and corrosion resistance for applications requiring durability under harsh conditions.
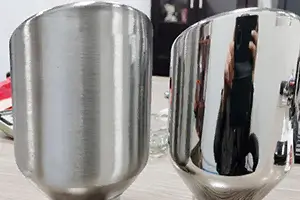
Polishing
Enhances the surface of parts by removing minor imperfections, resulting in a smooth and shiny finish that improves aesthetic appeal and surface cleanliness.
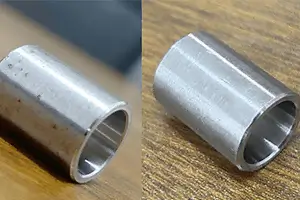
Passivation
Passivation enhances corrosion resistance by removing surface contaminants and forming a protective oxide layer. Ideal for stainless steel, it ensures durability, cleanliness, and long-term performance in industries like aerospace and medical devices.
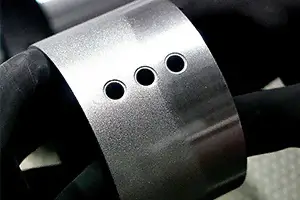
Sandblasting
Uses abrasive particles to create a uniform matte texture on the part’s surface, ideal for preparing parts for subsequent coatings or achieving a visually attractive finish.
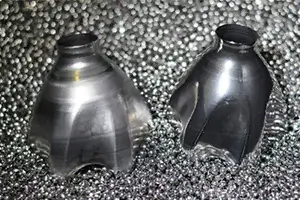
Tumbling
A mechanical finishing process that smoothens and polishes parts by rotating them in a tumbler with abrasives, suitable for deburring and improving surface texture.
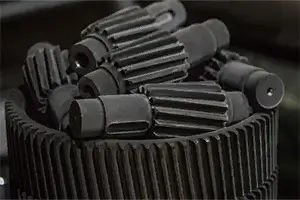
Heat Treatment
Enhances the mechanical properties of metal parts, such as hardness, toughness, and wear resistance, by heating and cooling them under controlled conditions.
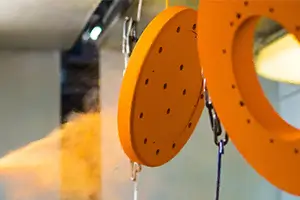
Powder Coating
Applies a durable and uniform layer of colored polymer powder, offering excellent protection against corrosion, UV damage, and general wear and tear.

Electroplating
A process of depositing a thin metal layer, such as nickel or chrome, onto a part’s surface to improve its appearance, corrosion resistance, and durability.
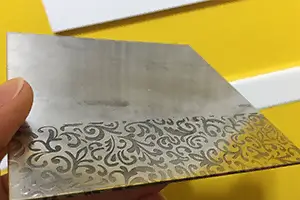
Laser Engraving
Uses focused laser beams to etch designs, text, or markings onto parts with high precision, providing permanent and highly detailed customizations.
Aluminum CNC Machining FAQ
Q: What industries benefit most from CNC-machined aluminum parts?
A: Industries such as aerospace, medical, automotive, and consumer electronics frequently use aluminum CNC machining due to its lightweight, strength, and adaptability.
Q: Are recycled aluminum materials available for machining?
A: Yes, upon request, we can source eco-friendly, recycled aluminum materials to support sustainable manufacturing practices.
Q: How do you ensure quality in aluminum CNC machining?
A: We implement rigorous quality checks, including dimensional inspections and surface integrity assessments, to meet precise specifications. Detailed reports are available upon request.
Q: What factors affect the cost of CNC aluminum parts?
A: Costs are influenced by material type, part complexity, tolerance requirements, and surface finishing. We provide competitive quotes tailored to your needs.
Q: Can aluminum parts be anodized in custom colors?
A: Yes, we offer anodizing in various colors to meet your aesthetic and functional requirements, with options for clear, black, red, and more.
Q: What information do I need to provide for an accurate quote?
A: Include your CAD files, material specifications, tolerance requirements, surface finish preferences, and desired quantity for a comprehensive and precise quote.