About the Magnesium
Magnesium is a lightweight metal known for its high strength-to-weight ratio, making it an ideal choice for industries such as aerospace, automotive, electronics, and medical devices. As the lightest structural metal, magnesium is 75% lighter than steel and 33% lighter than aluminum, yet it offers excellent mechanical properties and corrosion resistance when properly treated.
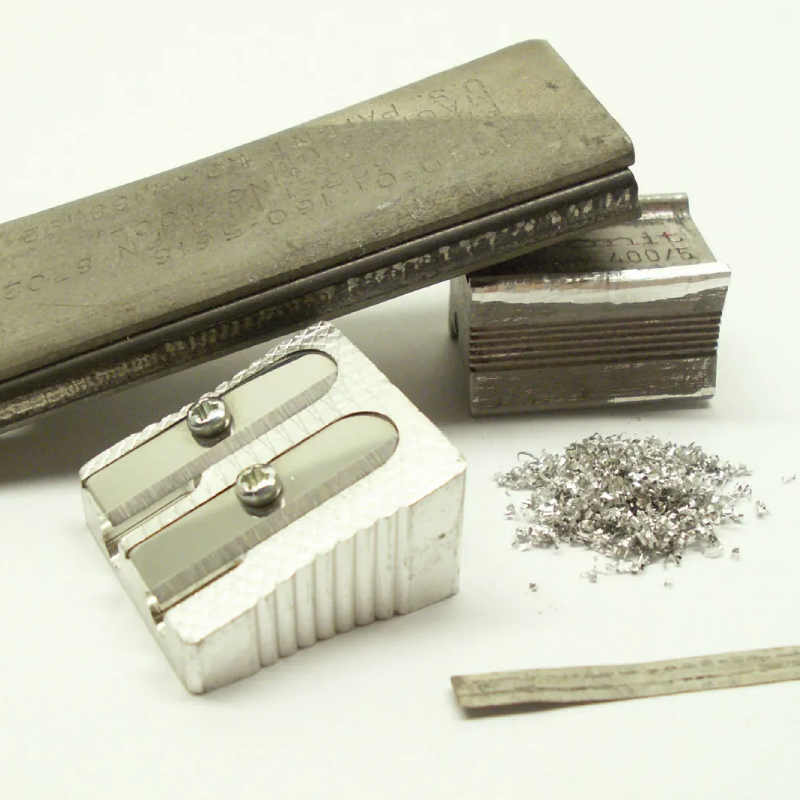
In CNC machining, magnesium stands out for its exceptional machinability. It allows for faster cutting speeds, reduced tool wear, and improved surface finishes compared to many other metals. Its versatility and ease of machining make it an efficient and cost-effective material for manufacturing complex, high-precision components.
·Lightweight and High Performance
·Excellent Machinability
·Precision in Complex Designs
·Thermal and Electromagnetic Properties
·Eco-Friendly Material
·Versatility in Surface Treatments
·Applications Across Industries
Customized Magnesium CNC Machining Services by JXD Precision
At JXD , we provide reliable CNC machining solutions for magnesium components, prioritizing safety, precision, and quality at every step. Our ISO9001-certified facility ensures exceptional accuracy, from prototypes to full-scale production. With expertise in milling, turning, and lathe machining, our skilled team delivers tailored support and clear communication to meet your exact requirements and achieve outstanding results.
Aspect | Details |
---|---|
Tolerances | Achievable machining tolerances depend on the specific magnesium alloy but typically reach up to ±0.005 inches (±0.127 mm). |
Wall Thickness | Minimum wall thickness of 0.03 inches (0.8 mm) is achievable, subject to the alloy type and ratio between thickness and part dimensions. |
Maximum Size | Maximum part dimensions of 2000 x 800 x 1000 mm are supported, accommodating a wide range of component sizes. |
Surface Finishes | Customizable surface finishes include polishing, anodizing, and coating for enhanced aesthetics and functionality. |
Supported Alloys | Commonly used magnesium alloys include AZ31, AZ61, and AZ91, with options for other grades on request. |
Machining Methods | Comprehensive services such as milling, turning, drilling, tapping, and threading to meet diverse requirements. |
Material Properties | Magnesium offers excellent strength-to-weight ratio, good thermal conductivity, and superior machinability. |
Lead Times | Standard lead times start from 7 days for commonly used magnesium alloys, with variations depending on complexity and production location. |
Volume Capability | Supports both low-volume prototyping and high-volume production, providing scalability for projects of all sizes. |
Packaging Options | Safe and customizable packaging to prevent oxidation and damage during shipping. |
Quality Assurance | Advanced inspection methods, including CMM (Coordinate Measuring Machine), ensure compliance with stringent quality standards. |
Environmental Safety | Magnesium is handled using specialized equipment and safety measures to ensure safe and sustainable processing. |
Optimized Comparison of Common Magnesium Alloys
Magnesium alloys combine lightweight properties, corrosion resistance, and machinability, making them perfect for aerospace, automotive, and industrial CNC machining projects.
Alloy | Ultimate Tensile Strength | Yield Strength | Elongation at Break | Elastic Modulus | Hardness (HV) | Key Features |
---|---|---|---|---|---|---|
Magnesium AZ31B | 260 MPa (37,700 psi) | 200 MPa (29,000 psi) | 0.15 | 44.8 GPa (6,498 ksi) | 88 | Lightweight with excellent machinability. Often anodized for corrosion resistance. An alternative to aluminum due to its strength-to-weight ratio and availability. |
Magnesium AZ91D | 240 - 250 MPa (35 - 36 ksi) | 160 MPa (23,200 psi) | 3 - 7% | 45 GPa (6,526 ksi) | 60 - 70 | High-purity die-cast alloy with excellent corrosion resistance, castability, and good strength. The most widely used magnesium die-casting alloy. |
Magnesium WE43 | 250 MPa (36,259 psi) | 220 - 250 MPa | 0.02 | 41 - 45 GPa | 85 - 105 | High-strength casting alloy suitable for temperatures up to 300°C (572°F). Known for good mechanical properties and corrosion resistance. |
Magnesium AM60B | 225 - 240 MPa (33 - 35 ksi) | 130 MPa (18,000 psi) | 8 - 13% | 45 GPa (6,526 ksi) | - | Superior ductility and energy absorption. Commonly used for automotive components due to its good strength and castability. |
Magnesium ZK60A | 365 MPa (52,900 psi) | 305 MPa (44,200 psi) | 0.11 | 44.8 GPa (6,498 ksi) | 100 | High strength and machinability but flammable during machining. Essential for aerospace parts like brake housings and landing gear. |
Magnesium QE22A - T6 | 260 MPa (37,700 psi) | 195 MPa (28,300 psi) | 0.03 | 45 GPa (6,530 ksi) | 90 | Casting alloy with excellent tensile strength, fatigue resistance, and creep properties at high and room temperatures. Weldable and pressure-tight. |
Magnesium Elektron 21 | 220 MPa (31,900 psi) | 175 MPa (25,400 psi) | 3 - 5% | 45 GPa (6,526 ksi) | 80 - 100 | Lightweight, with excellent fatigue strength and creep resistance. Widely used in aerospace and motorsport applications. |
Surface Finishing for CNC Machined Parts
JXD-Machining provides diverse surface finishing options to enhance the appearance, durability, and performance of CNC machined parts, meeting both functional and aesthetic needs.
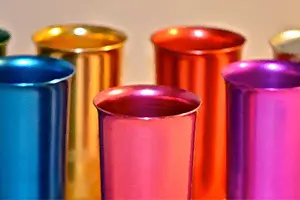
Anodizing
A durable and corrosion-resistant finish that enhances the aluminum part’s surface while providing an aesthetic appearance. Ideal for improving wear resistance and offering a wide range of color options.
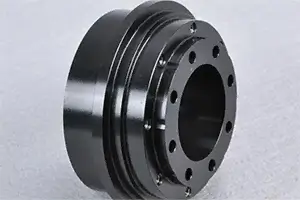
Black Oxide
A chemical coating that provides moderate corrosion resistance and a sleek black appearance, often used for steel parts to reduce glare and improve aesthetic appeal.
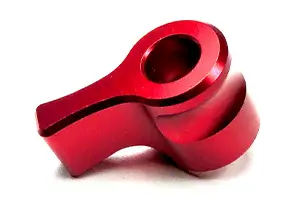
Sandblasting + Type II Anodizing
Combines a matte finish from sandblasting with Type II anodizing to create a smooth, uniform surface that is corrosion-resistant and visually appealing.
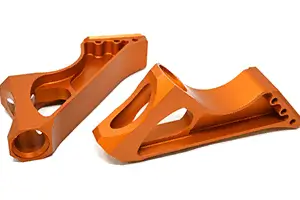
Sandblasting + Type III Anodizing (Hard Coat)
A more robust version of anodizing combined with sandblasting, offering excellent wear and corrosion resistance for applications requiring durability under harsh conditions.
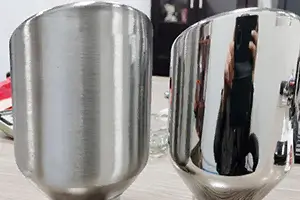
Polishing
Enhances the surface of parts by removing minor imperfections, resulting in a smooth and shiny finish that improves aesthetic appeal and surface cleanliness.
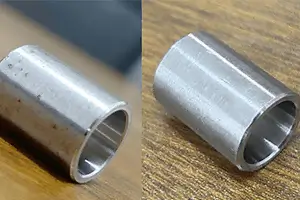
Passivation
Passivation enhances corrosion resistance by removing surface contaminants and forming a protective oxide layer. Ideal for stainless steel, it ensures durability, cleanliness, and long-term performance in industries like aerospace and medical devices.
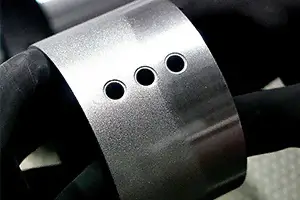
Sandblasting
Uses abrasive particles to create a uniform matte texture on the part’s surface, ideal for preparing parts for subsequent coatings or achieving a visually attractive finish.
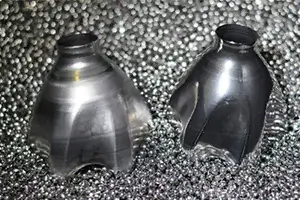
Tumbling
A mechanical finishing process that smoothens and polishes parts by rotating them in a tumbler with abrasives, suitable for deburring and improving surface texture.
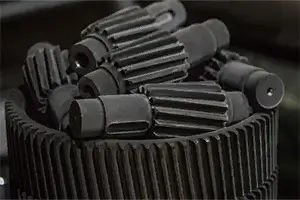
Heat Treatment
Enhances the mechanical properties of metal parts, such as hardness, toughness, and wear resistance, by heating and cooling them under controlled conditions.
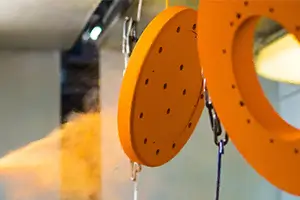
Powder Coating
Applies a durable and uniform layer of colored polymer powder, offering excellent protection against corrosion, UV damage, and general wear and tear.

Electroplating
A process of depositing a thin metal layer, such as nickel or chrome, onto a part’s surface to improve its appearance, corrosion resistance, and durability.
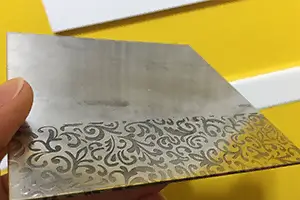
Laser Engraving
Uses focused laser beams to etch designs, text, or markings onto parts with high precision, providing permanent and highly detailed customizations.
Learn more about our metal and plastic surface finishing capabilities here.
FAQ for Magnesium CNC Machining Services
1. What are the benefits of using magnesium alloys for CNC machining?
Magnesium alloys are prized for their excellent strength-to-weight ratio, corrosion resistance, and machinability. These properties make them ideal for lightweight, durable components in aerospace, automotive, and industrial applications.
2. Which magnesium alloy is best for high-temperature applications?
Magnesium WE43 and QE22A are excellent choices for high-temperature applications, offering superior mechanical properties and resistance to creep and fatigue at elevated temperatures.
3. Are magnesium alloys suitable for marine applications?
Yes, magnesium alloys like AZ91D and AZ31B are commonly used in marine applications due to their corrosion resistance when anodized or properly treated.
4. How does CNC machining handle the flammability of magnesium?
Special precautions, such as using lubricants and fire suppression systems, are taken when machining magnesium to ensure safety and precision without compromising the material’s integrity.
5. Can magnesium alloys be combined with surface treatments?
Yes, magnesium alloys can undergo various surface treatments like anodizing, powder coating, and chromate conversion to enhance corrosion resistance, durability, and aesthetics.
6. Is magnesium machining cost-effective?
While magnesium offers excellent properties, its machining requires specialized care. However, its lightweight nature and performance benefits often justify the investment for high-performance applications.