Advanced Ceramic Machining Tailored to Your Needs
Specializing in high-precision ceramic machining, we deliver tailored solutions for complex projects. From small-batch production to prototype development, we ensure exceptional quality and reliability for every application
• Extensive experience in precision ceramic machining
• Support for small-batch production
• Fast quotes and sample services
• Technical support and end-to-end service
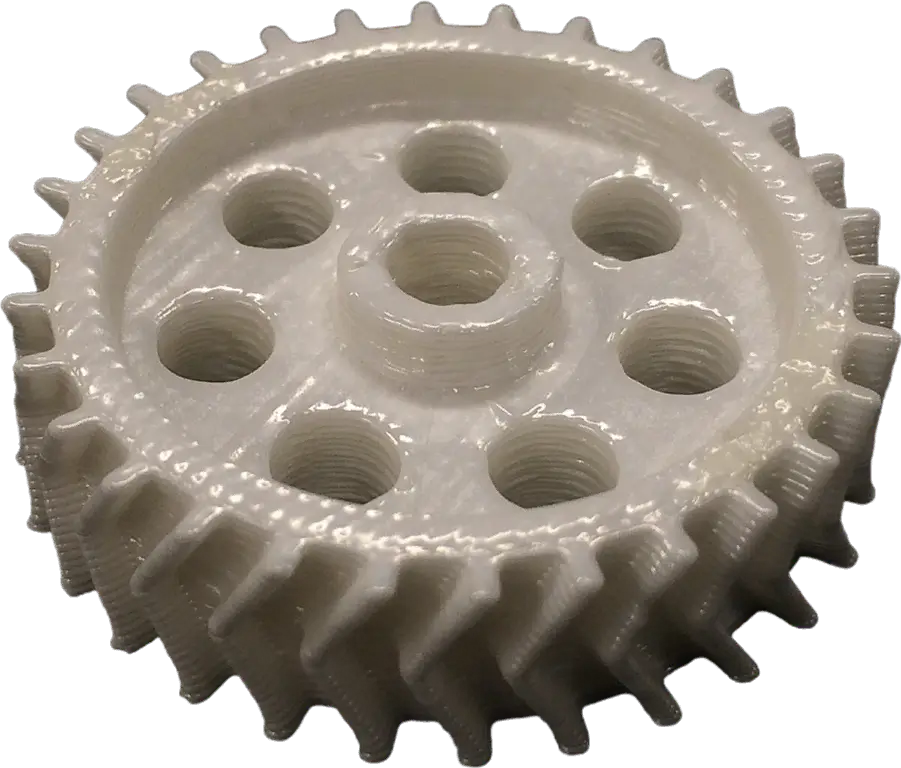
What is the Characteristics of Ceramic Material
Ceramic materials stand out with their exceptional hardness, thermal stability, and corrosion resistance, making them indispensable for high-performance applications in industries that demand reliability and precision.
Superior Hardness and Wear Resistance
Ceramic materials surpass metals and plastics in hardness, providing unmatched durability in high-friction and wear-intensive environments.
Outstanding Thermal Stability
With excellent performance under extreme temperatures, ceramics retain their strength and shape, making them ideal for high-heat applications.
Exceptional Corrosion Resistance
Ceramics resist chemical corrosion and oxidation, ensuring long-term performance in harsh or reactive environments.
Versatile Electrical Properties
Depending on the material, ceramics can act as excellent insulators or provide specific conductive properties, catering to diverse electronic requirements.
Lightweight yet Strong
Compared to metals, many ceramics offer significant weight reduction while maintaining strength and stability, perfect for aerospace and other lightweight-critical industries.
Biocompatibility
Certain ceramics are highly biocompatible, making them suitable for implants, surgical tools, and other medical applications.
Precision Tolerances for Complex Ceramic Parts
We provide precise machining tolerances for ceramic materials, ensuring exceptional quality and accuracy for your intricate components.
1. Standard Tolerances
For most ceramic parts, we achieve a dimensional tolerance of ±0.01 mm. This level of precision ensures consistent performance across various industries, including aerospace, medical devices, and electronics.
2. Custom Tolerances for Critical Components
For specialized applications, such as precision-engineered tools or components in high-stress environments, we can achieve tolerances as tight as ±0.005 mm, depending on the ceramic material and design complexity.
3. Surface Finishes
Ceramic surface finishes are equally critical to functionality. We offer a range of finishes, including smooth polishing up to Ra 0.2 µm, ensuring optimal performance for sealing surfaces, medical implants, or optical applications.
4. Hole and Slot Tolerances
For drilled or milled features such as holes and slots, we provide precise dimensional tolerances and clean edges, ensuring compatibility with assemblies and consistent quality.
5. Flatness and Roundness
For flat or cylindrical ceramic parts, we maintain strict flatness and roundness tolerances, ensuring alignment and fit for critical applications.
6. Material-Specific Adjustments
Tolerances may vary depending on the ceramic type (e.g., alumina, zirconia, or silicon carbide). Our engineers work closely with clients to optimize designs and ensure the achievable tolerances align with functional requirements.
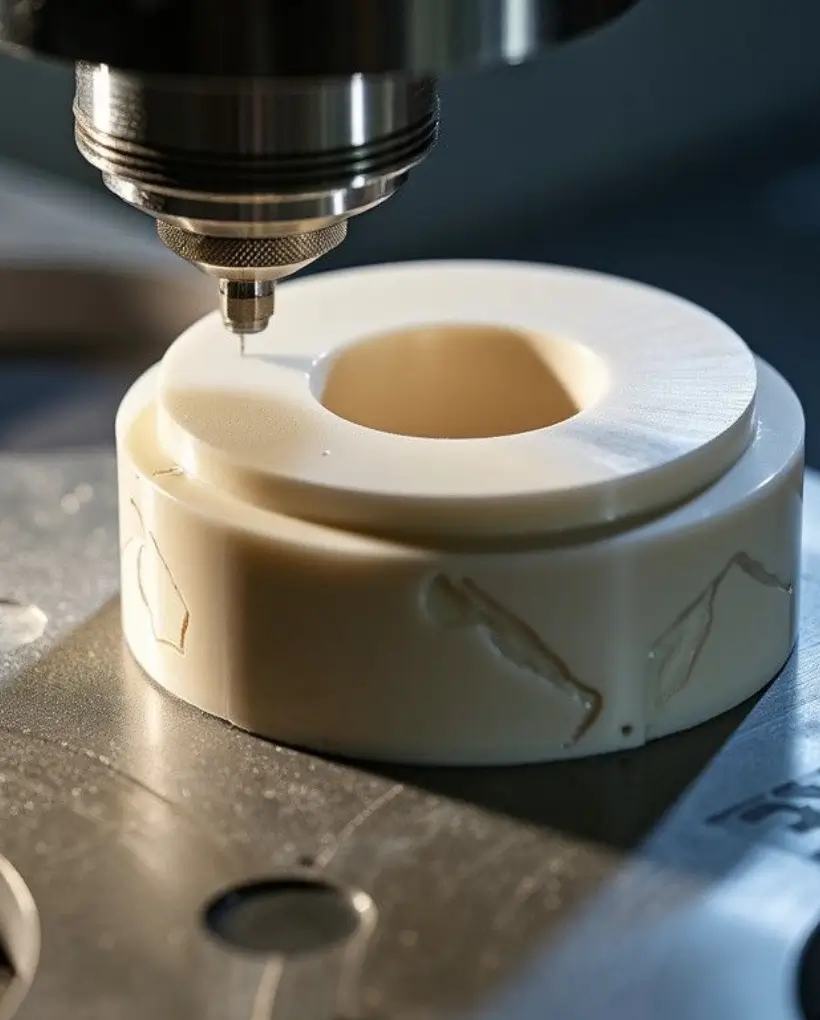
Key Properties of Advanced Ceramic Materials
Selecting the right ceramic material is key to achieving optimal performance and durability. Advanced ceramics offer unique properties like high strength, thermal stability, and wear resistance. Below is a summary of key characteristics to suit specialized industry needs.
Material | Compressive Strength (MPa) | Density (g/cm³) | Flexural Strength (MPa) | Fracture Toughness (MPa m1/2) | Hardness (GPa) | Max Temperature (°C) | Thermal Conductivity (W/m·K) | Thermal Expansion (10⁻⁶/K °C) |
---|---|---|---|---|---|---|---|---|
Zirconia | 2100 | 6.07 | 1400 | 17 | 14.5 | 1500 | 3 | 10 |
Alumina | 3500 | 3.98 | 650 | 4.5 | 18 | 1750 | 45 | 7.5 |
Aluminum Nitride | 3000 | 3.32 | 350 | 3 | 12 | 1200 | 230 | 4.55 |
Silicon Nitride | 3000 | 3.3 | 970 | 8.5 | 16 | 1400 | 28 | 1.9 |
Silicon Carbide | 2500 | 3.1 | 390 | 4.6 | 28 | 1900 | 102.6 | 4.02 |
Macor | 345 | 2.52 | 94 | 1.53 | 2.3 | 1000 | 1.46 | 9.3 |
Boron Nitride | 254 | 2.9 | 144 | N/A | N/A | 2000 | 130 | 4.1 |
Boron Carbide | 3000 | 2.8 | 420 | 4 | 33 | 1800 | 90 | N/A |
FAQ
Q: What are the main benefits of using ceramic materials for industrial applications?
Ceramic materials provide exceptional strength, thermal resistance, and wear resistance, making them ideal for demanding industrial environments. They are also lightweight and corrosion-resistant, offering longevity and efficiency.
Q: What is the typical lead time for ceramic machining and delivery?
Lead times vary based on material complexity and quantity, but rapid prototyping and small-batch production services can expedite the process.
Q: How do ceramic materials compare to metals and plastics?
Ceramics often outperform metals and plastics in areas like heat resistance, hardness, and wear resistance. However, they may be less ductile and require specialized machining.
Q: Can ceramics be customized for specific applications?
Yes, ceramics can be precisely machined and tailored to meet specific design requirements, including tight tolerances and complex geometries.
Q: Are ceramics resistant to chemical corrosion?
Many ceramics, such as boron nitride and aluminum nitride, offer excellent resistance to chemical corrosion, making them suitable for harsh chemical environments.