Copper CNC Machining Services
Offering durable, high-performance copper components with exacting specifications for various industries
● Certified Materials
● Factory Price
● No Minimum Order
● Fast Turnaround
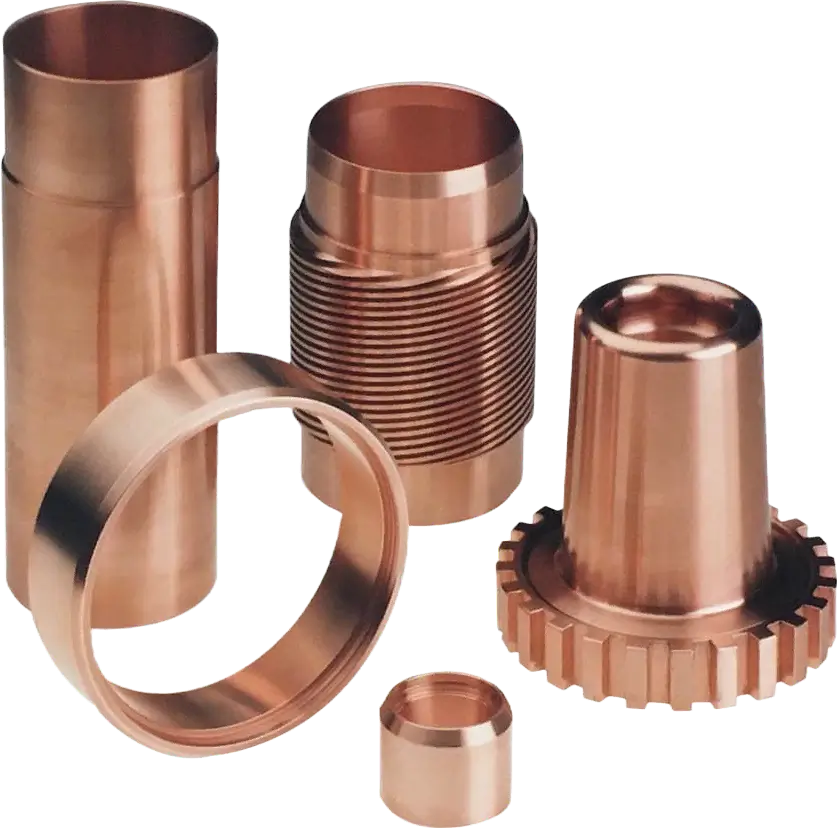
About Copper
Copper is one of the most widely used metals in CNC machining due to its exceptional electrical conductivity, thermal conductivity, and ease of machining. Known for its corrosion resistance and durability, copper is a versatile material used in a variety of industries, including electronics, power systems, automotive, and more.
Copper’s ability to handle heat and electricity efficiently makes it the ideal choice for components such as electrical connectors, circuit boards, and heat exchangers. With its excellent machinability, copper is easily shaped and fabricated into custom parts, allowing for precise specifications and superior performance in critical applications.
This material is also commonly used in industrial and manufacturing sectors for parts like fasteners, electrical wiring, and heat sinks. Its flexibility and range of uses are complemented by its non-corrosive properties, ensuring longevity and reliability in harsh environments.
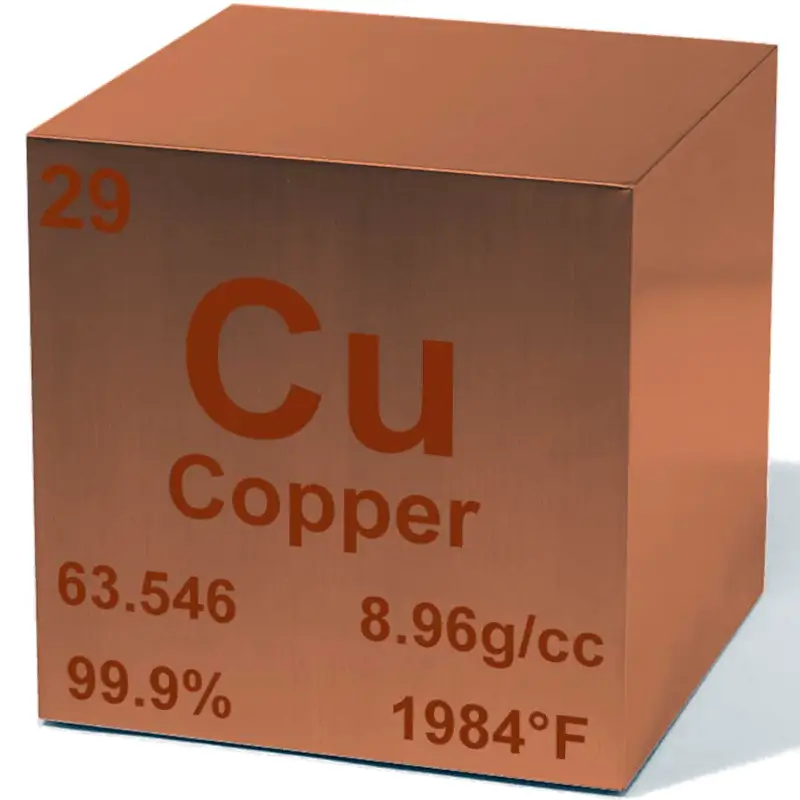
Common Copper for CNC Machining
Copper alloys are often selected based on their unique properties such as strength, machinability, and resistance to corrosion. The following table provides an overview of commonly used copper alloys and their characteristics, helping you choose the best material for your needs.
Copper Alloy | Ultimate Tensile Strength | Hardness | Thermal Conductivity | Applications |
---|---|---|---|---|
C11000 (Electrolytic copper) | 210 MPa (30,500 psi) | 70 HB | 390 W/m·K | Electrical contacts, Heat exchangers |
C26000 (Cartridge Brass) | 345 MPa (50,000 psi) | 70 HB | 120 W/m·K | Plumbing, Decorative hardware |
C17200 (Beryllium copper) | 1035 MPa (150,000 psi) | 210 HB | 120 W/m·K | Tools, Aerospace components, Electrical parts |
C68700 (Phosphor Bronze) | 480 MPa (70,000 psi) | 130 HB | 60 W/m·K | Marine components, Heavy-duty equipment |
C51000 (Spring copper) | 415 MPa (60,000 psi) | 180 HB | 90 W/m·K | Springs, Electrical connectors |
Copper Material Applications in CNC Machining
Copper’s unique combination of properties makes it suitable for a wide array of CNC machining applications. Whether you’re manufacturing electrical components or mechanical parts, copper alloys can meet the demands of your industry.
- Electrical Components
Copper is commonly used in wiring, connectors, and contacts due to its exceptional electrical conductivity.
- Heat Exchangers
Copper’s ability to efficiently conduct heat makes it perfect for use in heat exchangers and cooling systems.
- Plumbing and Hardware
Copper alloys like cartridge brass are ideal for plumbing fixtures and decorative hardware, offering both strength and corrosion resistance.
- Aerospace and Automotive
Copper alloys with enhanced strength are used for various components like tools, fasteners, and precision parts in demanding environments.
Copper Material Advantages for CNC Machining
Copper alloys offer a host of advantages, making them suitable for a wide range of industrial applications. With superior electrical and thermal conductivity, corrosion resistance, and machinability, copper is one of the top materials used in various industries.
- High Electrical Conductivity
Copper is ideal for electrical components that require excellent electrical conductivity.
- Corrosion Resistance
Copper’s resistance to corrosion, especially in marine environments, ensures long-lasting performance in harsh conditions.
- Thermal Conductivity
Copper’s excellent thermal conductivity makes it the go-to material for heat exchangers, cooling systems, and other heat-dissipating components.
- Good Machinability
Copper alloys are easy to machine, making them suitable for complex designs while ensuring high precision with minimal wear on tools.
FAQ
1. What copper alloys are suitable for CNC machining?
The most commonly used copper alloys for CNC machining include C11000 (electrolytic copper), C26000 (cartridge brass), C17200 (beryllium copper), and C51000 (spring copper). Each alloy has its unique properties tailored to different applications.
2. How do you ensure precision during copper machining?
We use high-precision CNC machines, and our team adheres to strict quality control measures to ensure all copper parts meet exact specifications. We work with tolerances as tight as ±0.01 mm.
3. What surface finishes can be applied to copper parts?
We offer various surface finishes for copper, including polishing, bead blasting, anodizing, passivation, and electroplating, depending on the requirements of your project.
4. What industries use copper for CNC machining?
Copper is widely used in industries such as electrical, automotive, aerospace, and marine, particularly for applications that require excellent electrical conductivity and corrosion resistance.
5. What is the lead time for CNC machined copper parts?
Our standard lead time for prototypes and small batch production is 5-7 business days. Lead times may vary based on the complexity and quantity of the order.