Precision Steel CNC Machining for Durable, High-Performance Parts
At JXD, we offer expert CNC machining services for a wide range of steel materials, providing precision-crafted components for industries like aerospace, automotive, medical devices, and more
• High precision for critical applications
• Custom steel grades tailored to your needs
• Fast delivery with efficient production processes
• Competitive pricing for both small and large runs
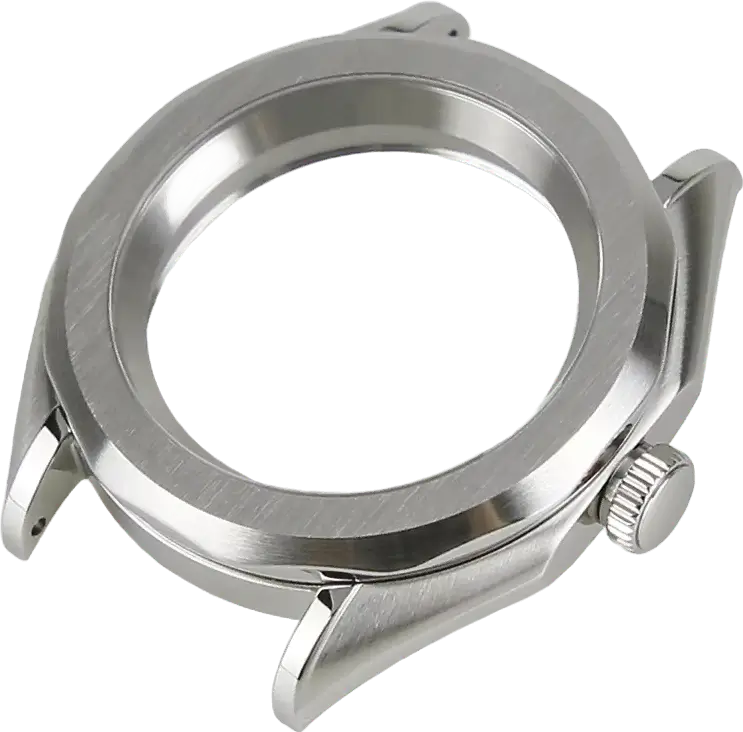
About Steel
Steel is one of the most versatile materials used in CNC machining. Known for its high strength, durability, and versatility, steel is widely used across industries for producing components that must endure high stress, extreme temperatures, and harsh environments. From automotive parts to structural components, steel offers outstanding mechanical properties that make it a top choice for manufacturing.
·High Strength
·High Ductility
·Good Machinability
·Corrosion Resistance
·Cost-effectiveness
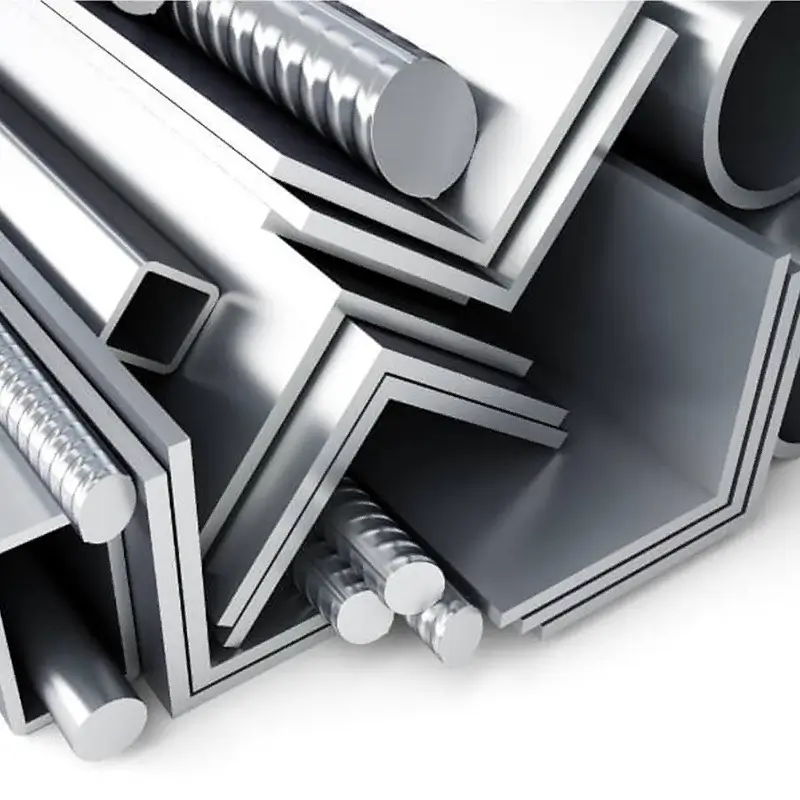
Common Steel Grades for CNC Machining
Selecting the right steel for CNC machining is crucial to ensuring the quality and performance of parts. Different types of steel offer varying mechanical properties and durability, making them suitable for different industries and applications. Below are some of the most common steel grades, each with its unique characteristics and areas of application, designed to meet diverse machining needs and design specifications.
Comparing Steel Grades for Optimal CNC Machining Performance
Different steel grades offer distinct advantages based on your project requirements. Below is a comparison of some of the most commonly used steel grades in CNC machining, including their features and ideal applications
Steel Grade | Strength | Hardness | Corrosion Resistance | Weldability | Common Applications | Characteristics |
---|---|---|---|---|---|---|
1018 Steel | Medium | 101 HRB | Low | Excellent | Automotive parts, shafts, structural components | Good machinability, cost-effective, ideal for general machining. |
304 Stainless Steel | High | 92 HRB | Excellent | Good | Food processing, medical equipment, marine components | Highly corrosion-resistant, non-magnetic, ideal for harsh environments. |
4140 Steel | High | 28-34 HRC | Moderate | Moderate | Aerospace, automotive, tools | Excellent fatigue resistance and strength at high temperatures. |
A36 Steel | Medium | 56 HRB | Moderate | Good | Structural steel, bridges, heavy machinery | Low carbon steel, versatile, used for general structural purposes. |
O1 Tool Steel | High | 60-62 HRC | Low | Poor | Cutting tools, molds, dies | Excellent wear resistance, high hardness after heat treatment. |
S7 Tool Steel | High | 54-58 HRC | Moderate | Moderate | Stamping tools, die casting | Excellent shock resistance, used for heavy-duty tools. |
D2 Tool Steel | Very High | 58-60 HRC | Low | Poor | Industrial blades, shear knives | Very high wear resistance, ideal for cutting tools. |
316 Stainless Steel | High | 95 HRB | Excellent | Moderate | Chemical processing, pharmaceuticals | Superior corrosion resistance, especially against chloride environments. |
JXD-Machining Steel CNC Machining Capabilities and Services
Our machining facility is ISO 9001 certified, ensuring unmatched design accuracy—whether you’re in need of rapid prototyping or full-scale production for end-use parts. With us, you can expect fast turnaround times in a reliable environment!
We have a skilled team specializing in CNC services, including milling, turning, and lathe machining. Additionally, we offer customized pricing based on your product’s development phase to maximize value in the shortest time possible. No matter your needs, our knowledgeable staff provides personalized support and will guide your project every step of the way.
Tolerances
Our achievable machining tolerances typically reach as tight as ±0.005 inches, depending on the specific type of steel used for your components.
Wall Thickness
We can achieve a minimum wall thickness of 0.03 inches (0.8 mm), although this may vary based on the ratio of wall thickness to part dimensions and the type of steel.
Maximum Part Size
We can accommodate parts up to 2000 x 800 x 1000 mm in size.
Lead Time
The shortest lead time for commonly used steels is 5 days, but this may vary depending on the specific material and whether the parts are being produced internationally.
Precision & Reliability
As a leading CNC machining provider, we guarantee precise parts, meeting stringent specifications and industry standards.
Expert Support
Our knowledgeable team works with you from concept to completion, providing expert guidance to ensure optimal results.
Surface Finishes For CNC Machined Steel Parts
JXD-Machining can provide the perfect finishing touch to your CNC machined Steel parts with a range of powder coating, bead blasting, and plating options. Each finish offers its own advantages – so make sure you select the one that meets all your requirements!
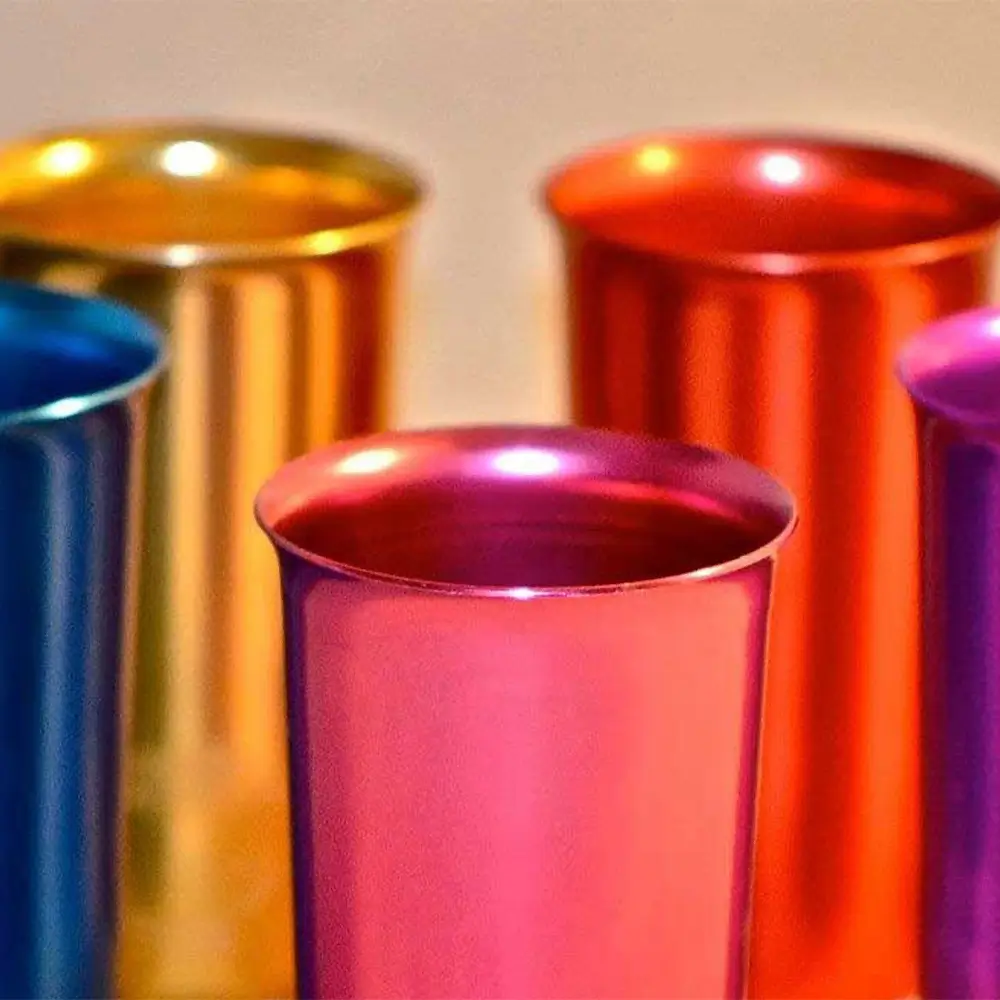
Anodizing
Anodizing creates a durable oxide layer on the surface of steel, increasing resistance to corrosion, wear, and environmental conditions. It also allows for coloring, enhancing both aesthetic appeal and functionality while maintaining the steel’s durability.
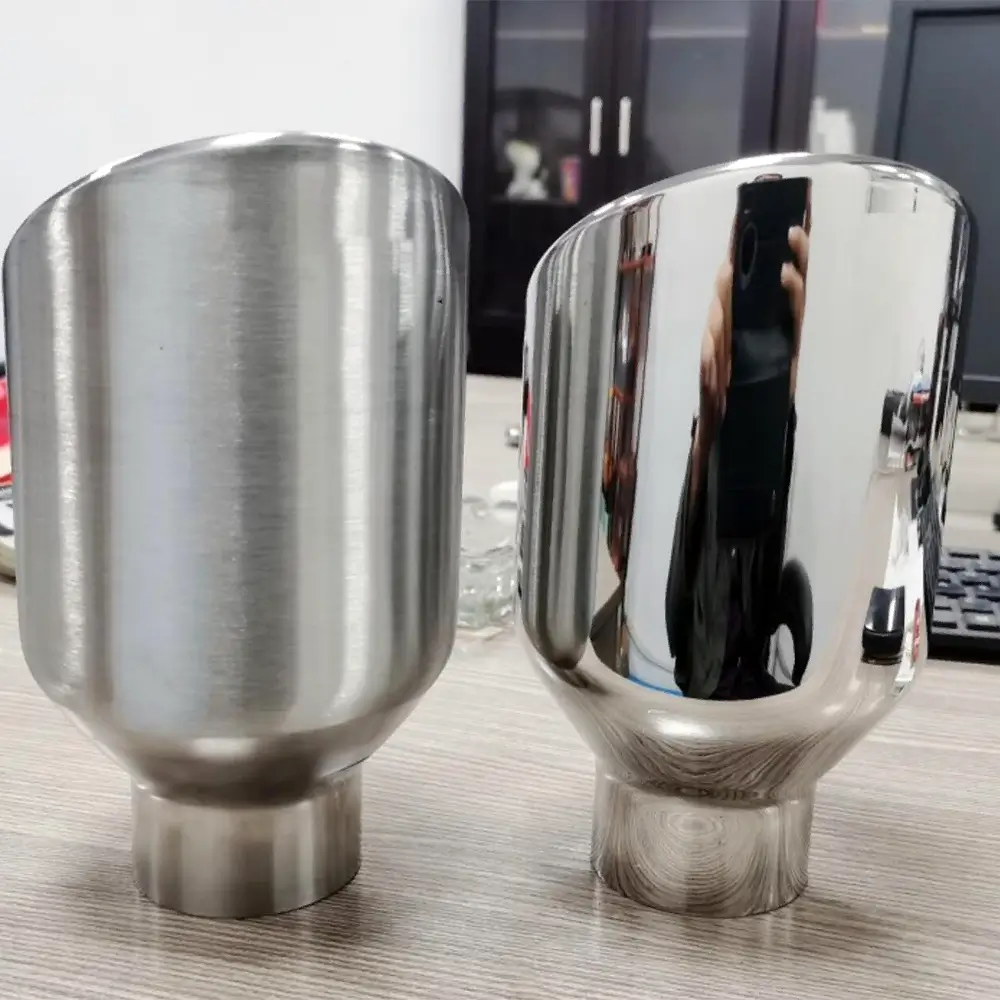
Polishing
Polishing smoothens the surface of steel parts, eliminating imperfections and providing a reflective, shiny finish. This process improves visual appeal and ensures that the parts meet the required surface quality standards.
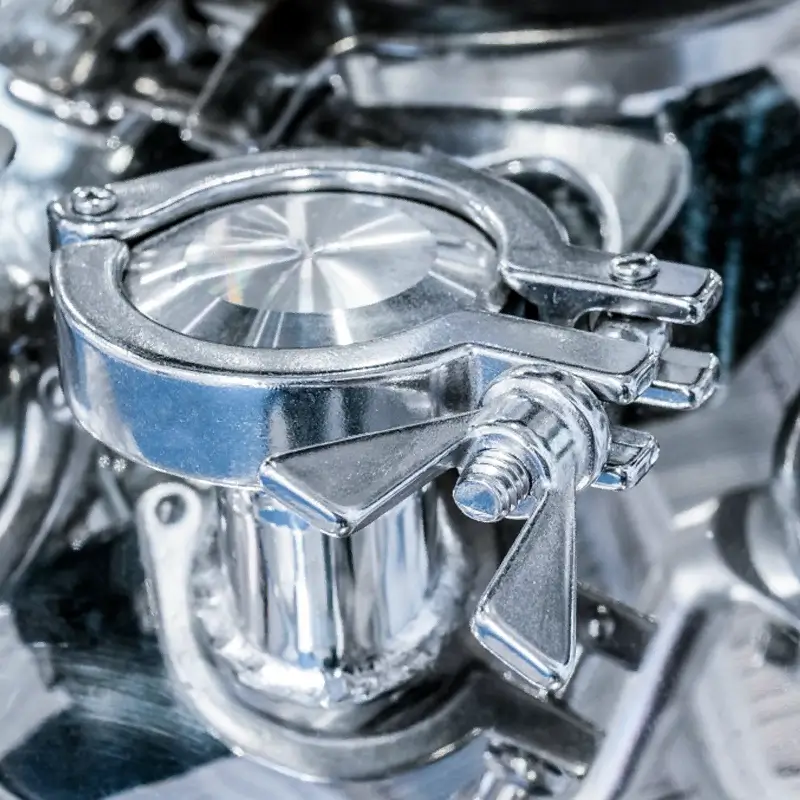
Passivation
Passivation forms a thin protective oxide layer on steel, improving its resistance to corrosion and enhancing its biocompatibility. This treatment is commonly used for parts exposed to harsh environments or for applications where durability and safety are crucial.
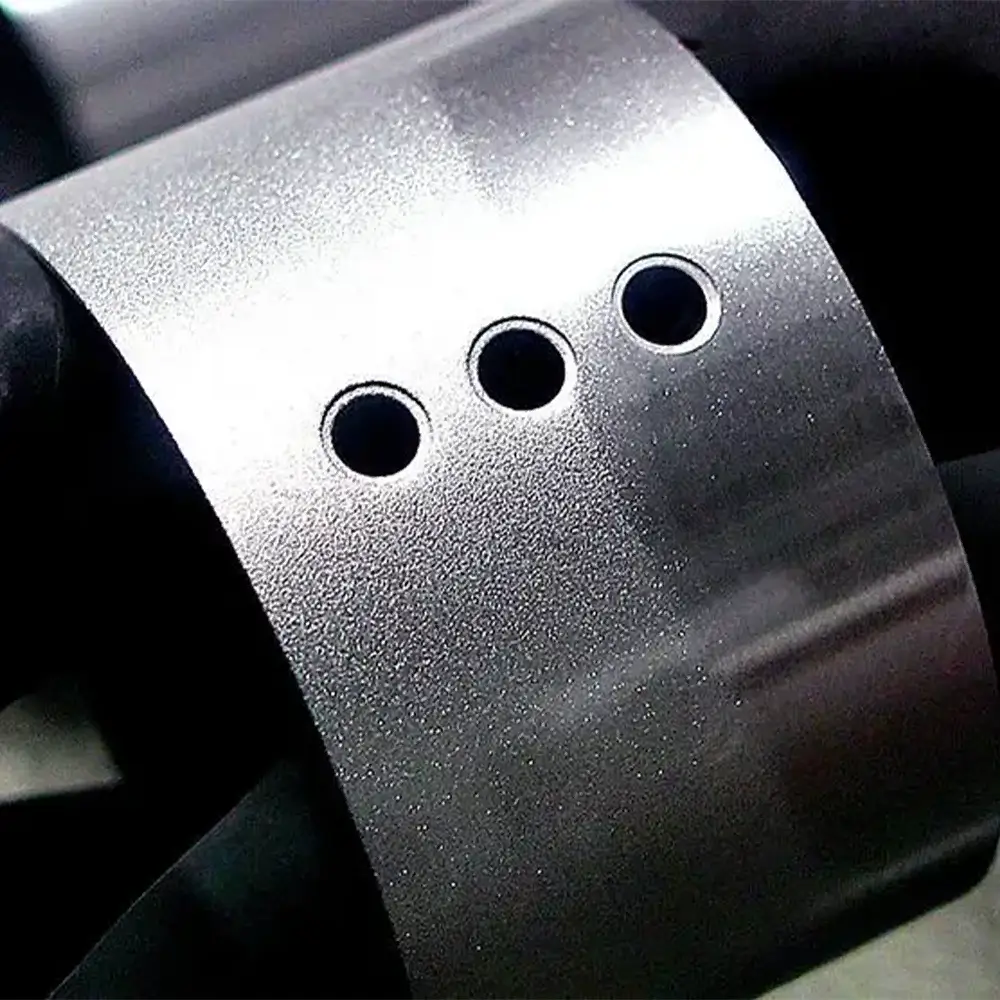
Bead Blasting
Bead blasting involves the use of small glass or ceramic beads propelled at high speed onto steel surfaces. This technique creates a consistent matte finish, improving the surface texture and reducing reflectivity, which enhances the part’s overall refinement.
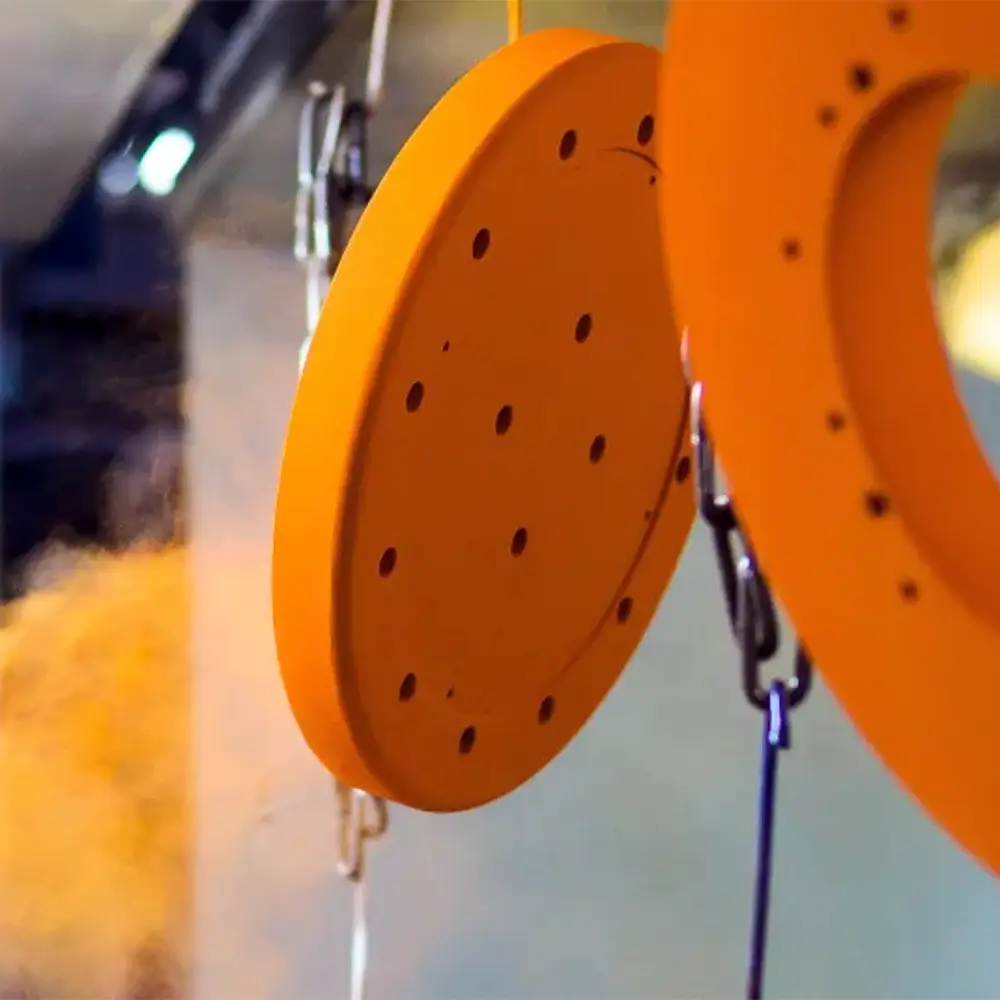
Powder Coating
Powder coating applies a dry powder to steel surfaces, which is then baked to create a tough, corrosion-resistant finish. This treatment offers a durable and long-lasting solution that also adds color to steel parts.
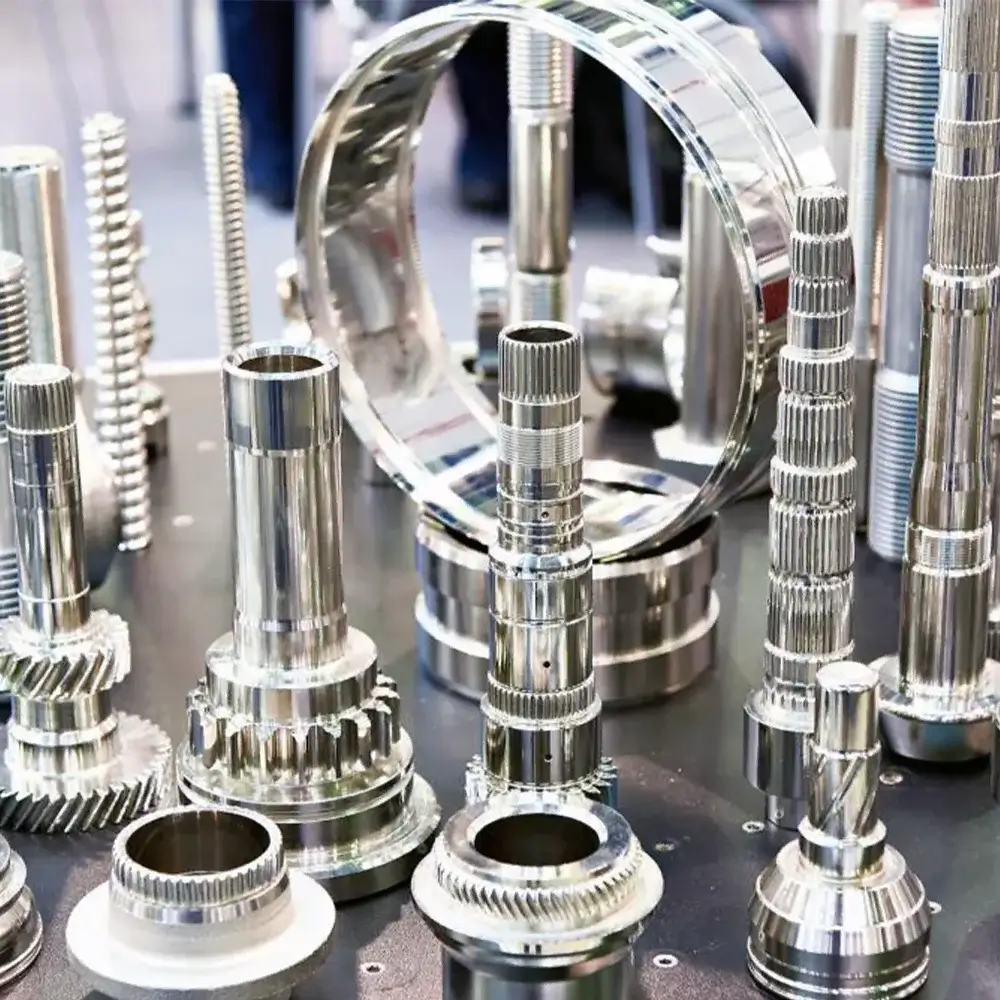
Plating
Plating involves applying a thin metal coating to the surface of steel to improve appearance, enhance corrosion resistance, or provide additional material properties like increased conductivity. This process is tailored to meet the specific requirements of the part.
Learn more about our metal and plastic surface finishing capabilities here.
FAQ
Q1: What is the best steel for CNC machining?
A1: The best steel depends on the specific application. For general purposes, steel grades like 1018 or 1045 are excellent choices. If high corrosion resistance is required, stainless steel grades like 304 or 316 are recommended. For high-strength applications, alloy steels like 4140 are preferred.
Q2: Can steel be used for both prototypes and mass production?
A2: Yes, steel is highly versatile and suitable for both prototyping and mass production. Steel’s durability and availability make it an ideal choice for custom machining in both small and large quantities.
Q3: How long does it take to machine steel parts?
A3: The machining time for steel parts depends on the complexity of the part and the type of steel used. Typically, we provide estimated lead times ranging from 5-15 business days for prototypes, with larger orders requiring additional time based on quantity and complexity.
Q4: How do you ensure the quality of machined steel parts?
A4: We utilize advanced quality control measures, including dimensional inspections, surface finish testing, and material verification, to ensure the final steel parts meet exact specifications.
Q5: Can you machine hardened steel?
A5: Yes, we can machine hardened steel using specialized tools and techniques that ensure precision and quality. For hard steels, we employ techniques like slow speeds and cutting-edge tool materials to achieve the desired finish without compromising the integrity of the material.