In the era of energy transition and industrial upgrading, wind turbine blades—core components for energy conversion—demand unprecedented manufacturing precision to ensure equipment efficiency and reliability. As a specialized CNC machining factory with deep expertise, we’ve delivered over 100,000 high-precision blades to global clients in wind power, industrial fans, and aerospace. This article dissects the core value of CNC machining for wind blades—from technological breakthroughs and process innovations to material applications and industry trends—empowering you to leverage the future of precision manufacturing.
5-Axis Machining: From Micron-Level Precision to Complex Geometry Fabrication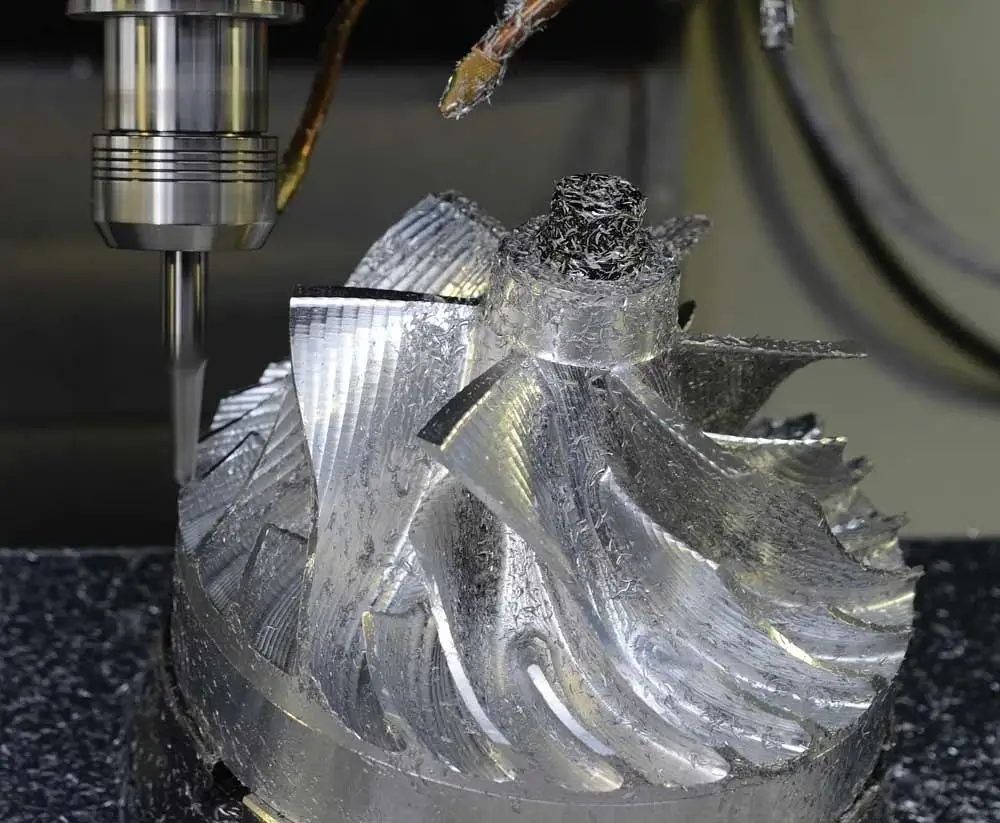
1. Technical Edge: Three Core Advantages of 5-Axis Machining Centers
·Dynamic Precision Control: Using Heidenhain CNC systems and laser tool probes, we achieve ±0.005mm positioning accuracy—60% lower error than traditional 3-axis machines.
·Curved Surface Mastery: With A/C dual rotary tables, we complete single-setup machining of wind blades with 12° twist angles and 0.8μm surface roughness, eliminating multi-step assembly.
·Intelligent Machining: An AI-driven cutting parameter optimization system extends tool life by 20% and boosts machining efficiency by 35%.
Case Study: For a high-speed centrifugal fan impeller, our 5-axis machining enabled stable operation at 130,000 RPM with ≤3mg dynamic balance precision—70% lower vibration than casting processes.
2. One-Piece Fabrication of Complex Structures
·Integrated Impeller Machining: From 20mm micro-impellers to 1.2m industrial fan impellers, 5-axis milling integrates hubs, blades, and shafts in one piece, reducing assembly errors.
·Lightweight Design: Topology optimization cuts aluminum alloy blade weight by 30% and carbon fiber composite blade weight by 45% without compromising strength.
Materials & Processes: From Traditional Metals to Advanced Composites
1. Science Behind Material Selection
Material |
Typical Applications |
Key Properties |
Machining Challenges |
Aluminum 6061 |
Industrial fan impellers, blowers |
Tensile strength 276MPa, density 2.7g/cm³ |
Tool wear control (diamond-coated tools) |
Titanium TC4 |
Aerospace impellers, high-temperature parts |
Tensile strength 895MPa, temp resistance ≤600℃ |
Heat management (high-pressure cooling) |
Carbon Fiber CFRP |
Wind turbine blades, UAV rotors |
Elastic modulus 230GPa, 4x specific strength of steel |
Delamination prevention (low feed rate + vacuum fixtures) |
2. Full Precision Machining Workflow
1. CAD Modeling: Aerodynamic optimization via UG NX, validated by CFD simulations to increase air volume by 15%.
2. CAM Programming: Helical interpolation paths at 8,000 RPM spindle speed and 1,200mm/min feed rate reduce toolpath repetition.
3. Rough Machining: Remove 90% material with a Φ20mm corn mill, leaving 0.5mm finishing allowance.
4. Finish Machining: Switch to a Φ8mm ball end mill with trochoidal milling for Ra≤0.4μm surface roughness.
5. Surface Treatment:
· Anodizing: 25μm oxide layer on aluminum, hardness HV≥300, salt spray resistance 1,000+ hours.
· Laser Cladding: Tungsten carbide coating on blade tips boosts wear resistance 5x, extending service life to 8 years.
Quality Control: From CMM Inspection to Full Lifecycle Management
1. Three-Tier Inspection System
· First Article Inspection: Zeiss CMM conducts 200+ dimensional checks, achieving ≥99.5% pass rate.
· Batch Sampling: 5% random sampling tested via vibration analysis for ≤2.8mm/s vibration (ISO 10816 standard).
· NDT (Non-Destructive Testing): Ultrasonic and magnetic particle inspection detect 99.9% of internal defects like cracks.
2. Data-Driven Process Optimization
· Machining Parameter Database: Over 1,000 parameter sets for materials, tools, and conditions enable rapid process reuse.
· Predictive Maintenance: Machine-to-Machine (M2M) monitoring tracks spindle load and tool wear, with 92% early-warning accuracy.
Industry Applications & Technology Comparison
1. Deep Adaptation to Typical Scenarios
Wind Power Sector:
·100m+ Blades: 5-axis machining ensures millimeter-level layup precision for 70-layer root sections, controlling weight under 30 tons.
· Lightweight Trend: CFRP blades paired with CNC machining reduce weight by 15%, increasing power generation efficiency by 8%.
Industrial Fans:
· Corrosion Resistance: 316L stainless steel with passivation handles pH 2–12 environments.
· Low-Noise Design: Aerodynamic simulations reduce noise by 10dB, meeting ISO 3744 standards.
2. Efficiency Comparison with Traditional Processes
Process |
Single-Piece Time |
Material Utilization |
Complex Geometry Support |
Cost (100–1,000 Units) |
CNC Machining |
4–8 hours |
80% |
Full support |
$20–$50/unit |
Casting |
24–48 hours |
50% |
Limited |
$10–$30/unit |
3D Printing |
12–24 hours |
95% |
Full support |
$80–$150/unit |
Industry Trends & Technological Innovations
1. Smart Manufacturing Upgrades
· Digital Twin Technology: Virtual process modeling reduces trial-and-error costs by 30% through pre-machining simulation.
· Automated Production Lines: Robotized loading/unloading enables 24/7 unmanned operation, increasing 产能 by 40%.
2. Green Manufacturing Practices
· Material Recycling: Glass fiber recovery ≥90%, carbon fiber recovery ≥85% for composite waste.
· Energy Savings: Low-power spindles (≤15kW) cut annual carbon emissions by 12 tons per machine.
3. Frontier Material Exploration
· Nano-Coatings: 5–10μm ceramic coatings on blades enhance corrosion resistance 5x, ideal for offshore wind environments.
· Shape Memory Alloys: Adaptive blades adjust angles with wind speed, boosting power efficiency by 12%.
5 Key Considerations When Choosing a CNC Machining Partner
1. Equipment Strength: Prioritize factories with 5-axis machines (e.g., DMG MORI DMU 80P) and high-precision inspection tools.
2. Process Expertise: Evaluate project cases in wind blades and aerospace impellers; request machining parameters and test reports.
3. Cost Control: CNC offers 30% higher material utilization than casting, with significant cost advantages for mid-lot production (100–1,000 units).
4. Rapid Response: 3-day prototype delivery, 7-day batch production, and emergency order support.
5. Value-Added Services: Comprehensive solutions including dynamic balancing, life prediction, and reverse engineering.
FAQ
Q: What is the minimum tolerance for CNC-machined wind blades?
A: 5-axis machining achieves ±0.005mm tolerance, suitable for aerospace-grade components.
Q: How to solve delamination in composite blade machining?
A: Use diamond-coated tools, low feed rates (≤500mm/min), and vacuum fixtures to prevent fiber breakage.
Q: How to ensure blade dynamic balance?
A: Laser trimming or counterweight adjustment via balancing machines achieves ≤2.8mm/s vibration.
Q: How does surface treatment impact blade performance?
A: Anodizing triples wear resistance; laser cladding extends lifespan to 8 years in harsh environments.
CNC machining for wind blades, driven by 5-axis technology, smart production, and material innovation, is becoming the industry standard. As a leading CNC manufacturer, we’re committed to delivering end-to-end solutions—from design optimization to mass production—with the philosophy of “Precision Drives Quality, Innovation Drives the Future.” Contact our experts today for a free consultation and customized quote.