In the intricate tapestry of materials science, ceramics have long held a position of significance. Their unique blend of properties – high hardness, exceptional heat resistance, and remarkable chemical stability – has rendered them indispensable across a diverse array of industries. From the high – tech environments of aerospace and electronics to the precise requirements of medical applications and the robust demands of the automotive sector, ceramics play a pivotal role.
However, the journey of shaping ceramics into useful components has not been without its challenges. Their inherent brittleness has, for years, posed a significant hurdle in the machining process. Enter Computer Numerical Control (CNC) machining, a technological marvel that has revolutionized ceramic manufacturing. This blog aims to take you on an in – depth exploration of ceramic CNC machining, covering every aspect from the fundamental nature of ceramic materials to the nuances of the machining process and its far – reaching applications.
Understanding Ceramic Materials
Oxide Ceramics
– Alumina ($Al_2O_3$) is a true workhorse among oxide ceramics. Its widespread use can be attributed to a remarkable set of properties. With a high hardness that ranks it among the top contenders in the material world, alumina is highly resistant to wear. This makes it an ideal choice for cutting tool inserts, where the constant abrasion from machining operations demands a material that can withstand the test of time.
– Zirconia ($ZrO_2$), on the other hand, brings a unique set of characteristics to the table. Its phase – transformation toughening mechanism sets it apart, endowing it with a relatively high level of toughness compared to other ceramics. This property has led to its adoption in applications such as dental implants, where it not only needs to be hard enough to function effectively but also resilient to withstand the forces exerted in the oral cavity.
Non – Oxide Ceramics
– Silicon carbide (SiC) is a material that has been making waves in the semiconductor industry. Its high thermal conductivity and extreme hardness make it a prime candidate for use in SiC wafers. In the context of machining, SiC – based ceramics are invaluable for high – speed cutting tools, as they can maintain their integrity even at elevated temperatures.
– Boron carbide ($B_4C$) holds the distinction of being one of the hardest materials known to man, second only to diamond. This extreme hardness, coupled with excellent wear resistance, has led to its use in applications where nothing less than the toughest materials will do, such as body armor and abrasive machining tools.
Key Properties of Ceramics
High Hardness
Ceramics are renowned for their high hardness values. Take alumina, for example, which can exhibit a Vickers hardness of around 15 – 20 GPa. This hardness is both a blessing and a curse. While it makes ceramics highly resistant to wear, it also presents a significant challenge during machining. Specialized tools and techniques are required to cut through these hard materials without causing damage.
Thermal Resistance
The ability of ceramics to withstand high temperatures is truly remarkable. Alumina, with a melting point of approximately 2050°C, can endure extreme heat without significant degradation. This property is of utmost importance in industries like aerospace, where components such as turbine engines are exposed to intense heat during operation.
Chemical Stability
Ceramics are like the fortresses of the material world when it comes to chemical stability. They can resist the corrosive effects of a wide range of chemicals, including acids and alkalis. This makes them an obvious choice for use in chemical processing plants, where components need to maintain their integrity in the face of harsh chemical environments.
Electrical Insulation
Most ceramics are excellent electrical insulators. Alumina, in particular, boasts a high electrical resistivity, making it a go – to material for electrical components such as insulators and substrates for electronic circuits. This property ensures the safe and efficient operation of electrical systems.
Basics of CNC Machining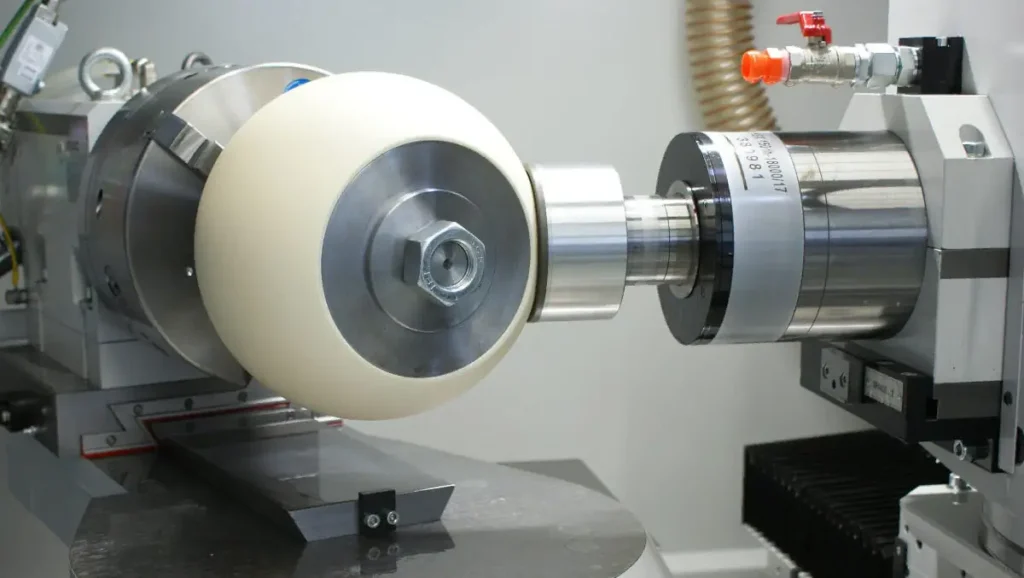
CNC machining is a manufacturing process that has transformed the way we produce components. At its core, pre – programmed computer software takes the reins, dictating the movement of factory tools and machinery. When it comes to ceramic machining, the precision and control offered by CNC machiningare nothing short of revolutionary.
The process begins with the creation of a 3D model of the desired ceramic component using computer – aided design (CAD) software. This digital blueprint is then translated into a set of instructions known as a G – code. The CNC machine reads and executes these instructions with incredible accuracy, allowing for the production of complex ceramic components with ease.
Components of a CNC Machine
Controller
– Think of the controller as the brain of the CNC machine. It is responsible for interpreting the G – code instructions and sending signals to the various axes of the machine, precisely controlling their movement. Modern CNC controllers are highly sophisticated, capable of making real – time adjustments based on feedback from sensors. This ensures that the machining process is not only accurate but also adaptable to changing conditions.
Machine Tool
– The machine tool is the physical structure that holds the cutting tools and the workpiece. Depending on the type of machining operation required, it can take the form of a milling machine, lathe, or grinder. In the case of ceramic machining, machines with high – speed spindles and rigid structures are preferred. These features enable the machine to handle the hard and brittle nature of ceramics effectively.
Cutting Tools
– The choice of cutting tools is a critical factor in ceramic CNC machining. Given the hardness of ceramics, diamond – coated tools are a popular choice. Polycrystalline diamond (PCD) tools, in particular, are highly valued for their exceptional wear resistance. However, selecting the right tool is not a one – size – fits – all approach. It requires careful consideration of the specific ceramic type and the machining operation at hand.
Ceramic Pre machining Considerations
Material Selection
The first step in any ceramic machining project is choosing the right material. This decision is not made lightly, as it depends on the intended application of the final component. For high – temperature applications, an oxide ceramic like alumina might be the top choice. If electrical properties are a primary concern, materials such as zirconia or certain oxide ceramics with specific electrical characteristics should be considered.
Design Optimization
The design of the ceramic component is where the real magic happens. It’s important to design the component in a way that takes into account the machining process. Sharp corners and thin walls should be avoided whenever possible, as they can create stress concentrations during machining, increasing the risk of cracking. Instead, fillets and rounded edges are preferred, as they help distribute stress more evenly.
Workpiece Preparation
Before the machining process can begin, the ceramic workpiece needs to be properly prepared. This often involves processes such as sintering, which helps achieve the desired density and hardness. Additionally, the surface of the workpiece should be flat and free from defects. Any imperfections on the surface can lead to inaccuracies in the machining process.
Ceramic Machining Operations
Cutting
Cutting ceramics is a delicate balancing act. Diamond – tipped saw blades or high – speed diamond – coated end mills are typically used for this purpose. However, the cutting speed and feed rate need to be carefully calibrated. When cutting alumina ceramics, for example, a relatively slow cutting speed of around 5 – 10 m/min may be employed. This slower speed helps prevent excessive heat generation, which can lead to cracking in the brittle ceramic material.
Drilling
Drilling holes in ceramics is no easy feat. Specialized diamond – coated drill bits are required, and the drill bit’s point angle is crucial. A proper point angle ensures smooth entry into the ceramic material. To further prevent issues such as chip clogging, a peck – drilling technique is often used. This involves periodically retracting the drill bit to clear the chips, allowing for a more efficient and accurate drilling process.
Milling is the key to creating complex shapes and features on ceramic components. High – speed milling with diamond – coated end mills can be highly effective, but it requires careful optimization of parameters. The depth of cut and feed rate need to be adjusted to avoid tool wear and damage to the workpiece. In the initial passes of milling a ceramic workpiece, a shallow depth of cut, such as 0.1 – 0.3 mm, may be used to gradually shape the material.
Grinding
Grinding is the final touch in the ceramic machining process, used to achieve the desired surface finish and dimensional accuracy. Diamond – based grinding wheels are the go – to choice for this operation. The grinding process can be divided into two main stages: rough grinding, which removes a significant amount of material, and fine grinding, which polishes the surface to a high – quality finish.
Deburring
After machining, ceramic components often have burrs on their edges. These burrs can affect the functionality and aesthetics of the component, so they need to be removed. Deburring can be accomplished through various methods, such as using abrasive brushes, chemical etching, or ultrasonic cleaning. Each method has its own advantages and is chosen based on the specific requirements of the component.
Surface Finishing
To truly enhance the quality of the ceramic component, surface finishing processes are often employed. Polishing is a common technique used to reduce surface roughness and improve the overall aesthetic appearance. In the semiconductor industry, chemical – mechanical polishing (CMP) is used to achieve ultra – smooth surfaces on ceramic substrates, ensuring the proper functioning of electronic components.
Challenges in Ceramic CNC Machining and Solutions
Brittle Fracture
Ceramics’ brittle nature is both their strength and their Achilles’ heel. During machining, they are highly susceptible to brittle fracture. This can occur due to a variety of factors, including excessive stress concentrations, sudden changes in cutting forces, or improper tool geometry. Brittle fracture can ruin an otherwise perfectly machined workpiece, leading to increased production costs.
Preventing brittle fracture requires a multi – pronged approach. Firstly, cutting parameters need to be carefully optimized. Sometimes, using a lower cutting speed and a higher feed rate can help reduce the likelihood of brittle fracture. Secondly, tool geometry plays a crucial role. Tools with rounded edges can distribute cutting forces more evenly, minimizing stress concentrations and reducing the risk of fracture.
Tool Wear
The high hardness of ceramics takes a toll on cutting tools, causing significant wear during machining. Even diamond – coated tools, which are among the most durable options, experience wear over time. Excessive tool wear can lead to a loss of machining accuracy and surface quality, affecting the final product.
To combat tool wear, high – quality cutting tools with advanced coatings are essential. Some modern diamond coatings are designed to have better adhesion and wear resistance. Regular tool monitoring is also crucial. By keeping a close eye on tool wear, operators can replace tools at the appropriate time to maintain machining quality. Additionally, using a coolant during machining can help reduce the temperature at the tool – workpiece interface, thereby extending tool life.
Heat Generation
Machining ceramics generates a substantial amount of heat. The high hardness of the material and the friction between the tool and the workpiece contribute to this heat generation. Excessive heat can cause thermal stress in the ceramic, leading to cracking, and can also accelerate tool wear, compromising the machining process.
Coolants are a simple yet effective solution to heat generation. They help dissipate heat and flush away chips, improving the machining process. In some cases, cryogenic machining, which involves using liquid nitrogen to cool the tool and workpiece, can be employed for more efficient heat removal. This technique can significantly reduce the negative effects of heat on both the ceramic material and the cutting tool.
Applications of Ceramic CNC Machined Components
Aerospace Industry
1. Engine Components
– In the aerospace industry, where every ounce of weight and every degree of efficiency matter, ceramic components machined by CNC are a game – changer. Ceramic turbine blades, for example, can withstand higher temperatures than their metal counterparts. This allows engines to operate more efficiently, consuming less fuel and producing fewer emissions. CNC machining enables the precise shaping of these complex – shaped blades to meet the exacting aerodynamic requirements of aerospace engines.
2. Thermal Protection Systems
– When a spacecraft re – enters the Earth’s atmosphere, it is subjected to intense heat. Ceramic – based thermal protection systems, made up of CNC – machined ceramic tiles, are crucial for protecting the spacecraft. These tiles need to be precisely shaped to fit the contours of the spacecraft, and CNC machining ensures that they are manufactured with the required dimensions and surface finish, providing reliable protection during re – entry.
Electronics Industry
1. Substrates
– The electronics industry relies heavily on ceramic substrates for mounting integrated circuits. Alumina and zirconia ceramics are popular choices due to their excellent electrical insulation and thermal conductivity properties. CNC machining can create intricate patterns of holes and traces on these substrates, enabling the proper connection of electronic components. This precision is essential for the reliable operation of modern electronic devices.
2. Insulators
– Ceramic insulators play a vital role in isolating electrical components. CNC – machined ceramic insulators can be designed with complex shapes to fit specific electrical assemblies. Their high electrical resistivity and mechanical strength make them ideal for this application, ensuring the safety and efficiency of electrical systems.
Medical Industry
1. Dental Implants
– Zirconia dental implants have gained popularity in recent years due to their biocompatibility, aesthetic appeal, and mechanical properties. CNC machining is used to precisely shape these implants to fit the unique anatomy of each patient’s jawbone. This ability to create custom – designed implants has significantly improved the success rate of dental implant procedures, providing patients with a more natural – looking and functional solution.
2. Medical Devices
– Ceramics are also used in a variety of medical devices, from surgical instruments to components in diagnostic equipment. CNC machining ensures that these components are produced with the high precision required for medical applications. The biocompatibility and chemical stability of ceramics make them suitable for use in the human body, while CNC machining allows for the production of components that meet strict medical standards.
Automotive Industry
1. Engine Components
– In high – performance automotive engines, ceramic components can offer significant advantages. Ceramic pistons and cylinder liners, for example, can withstand higher temperatures and pressures, improving engine efficiency. CNC machining is used to manufacture these components with the precision needed for a proper fit within the engine, ensuring optimal performance.
2. Exhaust Systems
– Ceramic – based catalytic converters are an integral part of automotive exhaust systems. CNC machining is used to produce the ceramic substrates within these converters with the precise honeycomb – like structures required for efficient gas conversion. This helps reduce emissions and improve the environmental performance of vehicles.
Future Trends in Ceramic CNC Machining
Advanced Tooling Materials
1. Nanocomposite Tools
– The future of ceramic CNC machining looks promising with the development of nanocomposite tools. These tools, which incorporate nanoscale reinforcements, are expected to offer even higher levels of hardness, wear resistance, and toughness. For instance, tools with carbon nanotube – reinforced coatings may be able to withstand higher cutting forces and temperatures, enabling faster and more efficient machining of ceramics. This could revolutionize the production process, reducing costs and increasing productivity.
2. Self – Sharpening Tools
– Another exciting trend on the horizon is the development of self – sharpening tools for ceramic machining. These tools would be able to maintain their cutting edge geometry during machining, eliminating the need for frequent tool changes. This not only improves machining efficiency but also reduces production costs. Research is ongoing to perfect this technology, and it could have a significant impact on the ceramic machining industry.
Automation and Robotics
1. Automated Machining Cells
– The integration of CNC machining with automation and robotics is becoming increasingly common in ceramic manufacturing. Automated machining cells can perform multiple machining operations in sequence, with robots handling the loading and unloading of workpieces. This not only increases productivity but also improves the consistency of the machining process. The use of automation also reduces the risk of human error, ensuring higher – quality ceramic components.
2. Adaptive Control Systems
– Adaptive control systems are set to transform ceramic CNC machining. These systems use sensors to monitor the machining process in real – time and adjust the cutting parameters accordingly. For example, if tool wear is detected, the system can automatically adjust the feed rate or cutting speed to maintain machining accuracy. This level of intelligent control will lead to more efficient and precise ceramic machining, meeting the growing demands of various industries.
New Ceramic Materials and Composites
1. Functionally Graded Ceramics
– Functionally graded ceramics represent a new frontier in materials science. These ceramics have a gradual change in composition and properties across their volume. CNC machining will be essential in shaping these materials into useful components. They can be designed to have different properties in different regions, such as high hardness on the surface for wear resistance and better toughness in the core for impact resistance. This opens up new possibilities for applications in industries such as aerospace and automotive.
2. Hybrid Ceramic – Metal Composites
– The development of hybrid ceramic – metal composites is another exciting trend. These composites combine the best properties of ceramics and metals, such as the high hardness of ceramics and the ductility of metals. CNC machining will be required to machine these complex composites into components for a wide range of applications. This could lead to the creation of stronger, more versatile components in industries like aerospace, automotive, and medical.
Ceramic CNC machining has evolved into a sophisticated and indispensable manufacturing process. Despite the challenges posed by the brittle and hard nature of ceramics, continuous advancements in tooling, machining techniques, and process control have enabled the production of high – precision ceramic components across various industries.
As we look to the future, the trends in advanced tooling materials, automation, and the development of new ceramic materials and composites promise to further expand the capabilities of ceramic CNC machining. Whether it’s enhancing the performance of aerospace engines, powering the next generation of electronic devices, improving medical treatments, or revolutionizing the automotive industry, ceramic CNC machining will continue to play a pivotal role in driving innovation and progress. The journey of ceramic CNC machining is far from over, and the possibilities for the future are truly exciting.